The Humanoid Revolution Hits Factory Floors
What happens when human labor shortages collide with next-generation robotics? Manufacturing enters its most transformative decade since Henry Ford’s assembly line. In 2025, industrial humanoid robots transition from prototypes to production-line staples, with BMW, Tesla, and Amazon leading deployments. This shift addresses a critical problem: The National Association of Manufacturers reports 2.1 million unfilled U.S. factory jobs by 2030, costing $1 trillion annually in lost output.
Unlike single-task machines, humanoids leverage human-like dexterity to navigate existing infrastructure. Dr. Elena Rodriguez, MIT robotics researcher, notes that they’re the Swiss Army knives of automation. One platform handles palletizing, quality inspection, and machine tending—no facility redesign needed. For a deeper dive into how robotics addresses labor shortages, check out Why Robots Solve the Labor Crisis and What Stops Them for insights on barriers and solutions.
Section 1: Top 5 Industrial Humanoid Robots of 2025
1. Tesla Optimus Gen-2: The Scalable Workhorse
Deployment Site: Tesla Fremont Assembly Plant (California)
Primary Function: Battery module assembly and final vehicle inspection Standing 1.73m tall, Optimus handles delicate wiring harness installation with 0.5mm precision—a task previously requiring human finesse. Its breakthrough lies in real-time error recovery: When a misaligned component halts the line, Optimus diagnoses the issue, adjusts grip pressure, and completes the task without human intervention.
2025 Impact:
- Reduced battery module defects by 37% at Fremont
- Cut inspection time per vehicle from 90 to 22 seconds
- Production target: 5,000 units by Q4 2025 (Priced at $50,000/unit)
Carlos Mendez, Tesla Production Lead, emphasizes, Optimus isn’t replacing technicians—it’s multiplying their impact. One worker now supervises three robots handling hazardous high-voltage systems.
2. Agility Robotics’ Digit: Logistics Specialist
Deployment Site: Spanx Distribution Center (Georgia) & Amazon Rialto Warehouse (California)
Primary Function: Parcel sorting and palletizing Digit’s bird-inspired legs absorb impact when jumping off platforms, enabling 15kg payload transport across uneven floors. At Spanx’s Georgia hub, 12 Digits reduced box-handling labor costs by 40% during peak season. The system’s collaborative intelligence allows human workers to redirect tasks via voice command: “Digit, prioritize Category B shipments.”
Technical Edge:
- 4-hour continuous runtime with hot-swappable batteries
- Dynamic pathfinding around fallen objects or workers
- Injury reduction: 0 forklift collisions since deployment
For a closer look at how Amazon’s automation strategies are reshaping warehouses, explore Amazon’s Warehouse Automation: A Game-Changer or Job Killer? for a balanced analysis of efficiency versus employment impacts.
3. Apptronik Apollo: Heavy Payload Handler
Deployment Site: Mercedes-Benz Tuscaloosa Plant (Alabama)
Primary Function: Chassis component installation Apollo’s 25kg payload capacity tackles suspension and transmission mounting—operations requiring both strength and precision. Its modular joint system enables tool changes in under 90 seconds: magnetic grippers for metal parts, soft silicone claws for wiring. Hyundai Partnership: Testing Apollo for bumper installation in Seoul, where it reduced ergonomic injuries by 63% among workers previously handling bulky components.
4. Figure 02: Precision Assembly Expert
Deployment Site: BMW Spartanburg Plant (South Carolina)
Primary Function: Door seal installation and sheet metal alignment BMW deployed 15 Figure 02 units to handle sealant application—a task demanding consistent pressure control. Using haptic feedback sensors, the robot maintains 3.2 Newtons of force ±0.1N variance, eliminating leaks in 99.4% of vehicles versus 92% manually.
Training Innovation:
- Learns tasks via VR demonstrations by master technicians
- Reduced training time from 6 weeks to 48 hours
- 2025 target: 300 units across BMW’s global network
BMW’s precision manufacturing advancements are further explored in BMW Humanoid Robot Precision Manufacturing, detailing how these robots enhance production quality.
5. Boston Dynamics Electric Atlas: Non-Standard Material Specialist
Deployment Site: Hyundai Motor Group Metaplant (Georgia)
Primary Function: Handling irregular components Atlas maneuvers 18kg asymmetrical objects like dashboard assemblies through narrow aisles. Its proprietary balance algorithm recovers from collisions or slippery surfaces—addressing a historic limitation. Safety Advancement:
- Stops motion within 0 seconds of detecting human intrusion
- Force-limited joints prevent injury upon contact
- ISO/TS 15066 certified for close-proximity work
For more on Atlas’s role in construction and industrial settings, visit Boston Dynamics Atlas Humanoid Robots in Construction to see how it’s transforming non-traditional environments.
Section 2: Adoption Accelerators: Why 2025 Marks the Tipping Point
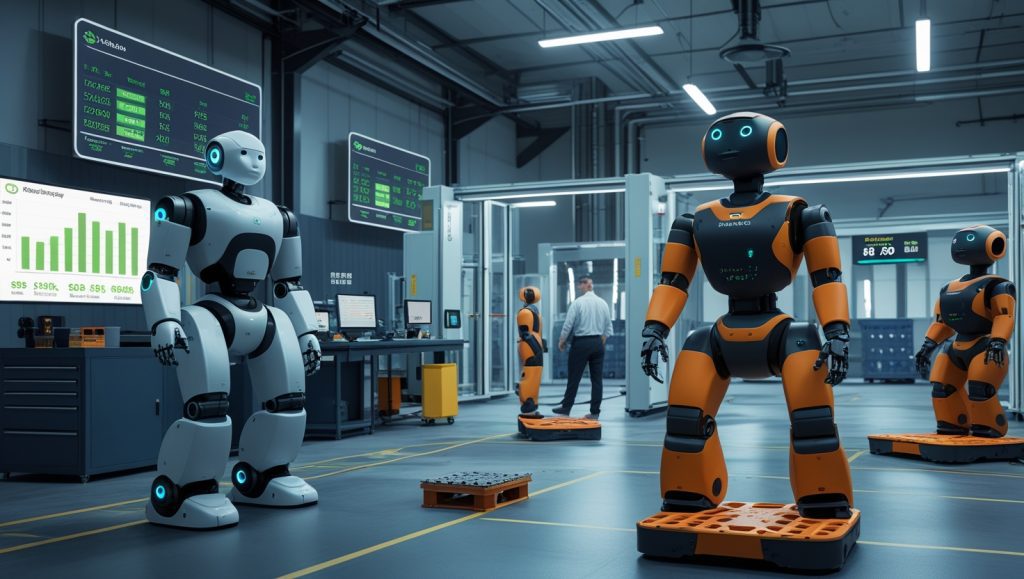
Labor Demographics Reaching Crisis Levels
- Automotive: 35% of skilled technicians retire by 2030 (Deloitte)
- Electronics: Foxconn struggles with 45% annual worker turnover
- Solution: Humanoids fill high-attrition roles—night shifts, hazardous tasks
Real-World Impact:
At Milwaukee Tool’s Tennessee plant, three Atlas units eliminated 3,200 monthly overtime hours previously required for heavy motor handling. Plant Manager Rajiv Soto notes, Workers focus on calibration now, not back strain.
AI Maturity Enables Unscripted Problem-Solving
Early models followed rigid paths. 2025 humanoids leverage:
- Meta’s V-JEPA 2: Predicts physical outcomes from video context
- NVIDIA Project GR00T: Trains robots via simulation scenarios
- 1X’s Redwood AI: Adapts to unseen obstacles in real-time
Result: Agility’s Digit navigates fallen pallets 87% faster than 2024 models. To understand how simulation-based training is slashing costs, read Physical AI Simulation Slash Robot Training Costs for a breakdown of its impact on robotics development.
Economic Viability Arrives
Cost Reduction Timeline:
Year | Avg. Unit Price | Key Driver |
---|---|---|
2022 | $250,000 | Custom R&D |
2024 | $120,000 | Modular design |
2025 | $80,000 | Tesla/BYD mass production |
2027 | $30,000 (est.) | Battery/actuator economies |
Leasing models democratize access:
- Apptronik Apollo: $11/hour per unit
- Agility Digit: $8/hour with maintenance included
For broader insights into the economic drivers behind humanoid robotics, Humanoid Robot Economics Driving $38B Industry Growth by 2035 offers a detailed forecast.
Section 3: Technical Barriers and 2025 Breakthroughs
Battery Endurance Solutions
Problem: 4-hour average runtime disrupts workflows
Innovations:
- Tesla’s conductive charging floors: 15-minute top-ups during idle periods
- Figure 02’s swappable packs: 90-second changeover
- MIT Solid-State Prototype: 8-hour runtime (Lab testing)
For a deeper look at energy-efficient robotics trends, check out Top 7 Energy-Efficient Robotics Trends Transforming Industries in 2025 for cutting-edge advancements in power management.
Dexterous Manipulation Advances
Sanctuary AI’s Phoenix demonstrates tactile sensitivity:
- Identifies material hardness via pressure sensors
- Adjusts grip force from 0.1N (circuit boards) to 300N (engine blocks)
Industrial Application: Samsung uses Phoenix prototypes for micro-soldering in Austin semiconductor lines. Safety Integration Standards
Updated ISO/TS 15066 mandates:
- Speed reduction zones when humans approach
- Torque monitoring to prevent crush injuries
- NEURA Robotics’ 4NE-1: Ultrasonic sensors detect workers within 5m
To explore safety concerns in greater detail, Humanoid Robot Safety Concerns Rise examines the challenges and solutions for safe human-robot collaboration. Section 4: Future Projections: 2026-2030 Roadmap
- 2026: Domain-specific variants emerge (construction, mining)
- 2027: AI “train-the-trainer” systems enable skill transfers between robots
- 2028: First fully autonomous humanoid factories (Foxconn prototype)
- 2030: 30% of repetitive industrial tasks handled by humanoids (McKinsey)
Economic Impact: Ark Invest forecasts $24 trillion in labor value displacement by 2035. For a glimpse into how robotics is reshaping industries beyond manufacturing, Robotics in Fashion: A Sustainable Revolution highlights innovative applications driving sustainability. To stay updated on global robotics trends, visit Robotics Business Review for the latest industry news and analysis.
FAQ: Industrial Humanoid Robots Explained
Can humanoids operate alongside humans safely?
Yes. ISO 15066-certified models like Atlas and Apollo feature force-limited joints and collision detection.
What’s the average payback period?
14 months at current leasing rates, based on 60% labor cost reduction in material handling.
Do they require specialized infrastructure?
No. They navigate existing factories using visual mapping, not magnetic tapes or reflectors.
Will this worsen unemployment?
BMW data shows redeployment: 80% of workers transition to robotics supervision or maintenance roles.
Strategic Imperatives for Manufacturers
Industrial humanoid robots solve 2025’s most urgent challenges: unsustainable labor gaps and precision demands. As Tesla and BMW demonstrate, early adopters gain decisive productivity advantages—Optimus Gen-2 achieves 98.4% uptime versus 82% for traditional automation.
Three Action Steps:
- Audit high-injury/high-turnover tasks for automation potential
- Pilot leased units (e.g., Digit at $8/hour) before capital investment
- Upskill technicians via robotics certification programs
Dr. Amelia Chen, Stanford Manufacturing Robotics Lab, sums it up: This isn’t about replacing humans—it’s about extending human capability. Robots handle torque wrenches; people handle problem-solving. Data Sources & Further Reading
- National Association of Manufacturers
- Ark Invest Economic Projections
Your Next Step?
Stay ahead in industrial automation. Subscribe for Robotics Deployment Updates or Download our Humanoid ROI Calculator (Coming Soon).