Imagine a factory floor where machines don’t just hum along—they dance. Robotic arms twist and turn, extruding material with surgical precision, while 3D printers churn out parts that defy the limits of traditional manufacturing. This isn’t science fiction; it’s the reality of robotics in 3D printing, a partnership that’s rewriting the rules of how we build things. From lightweight robot grippers to sprawling architectural structures, this synergy is proving to be a game-changer. But why is robotics in 3D printing such a big deal? Let’s dive into the five key reasons this fusion is unlocking unprecedented potential—and why it’s not all smooth sailing.
The marriage of robotics and 3D printing isn’t just a tech buzzword; it’s a seismic shift. Robotics in 3D printing brings automation, flexibility, and creativity to a process that was once rigid and wasteful. I remember visiting a small robotics startup in Shenzhen a few years back. The founder, a wiry guy named Li, showed me a robotic arm printing a drone frame in one fluid motion—no molds, no assembly lines, just raw efficiency. “This,” he said, grinning, “is what freedom looks like.” His words stuck with me because they captured the essence of what’s happening here: robotics in 3D printing is unshackling innovation from old constraints.
But it’s not all rosy. The tech has its hiccups—costly hardware, steep learning curves, and occasional flops that leave engineers scratching their heads. Still, the promise outweighs the pitfalls. In this 6000-word deep dive, we’ll explore why robotics in 3D printing is the key to unlocking the future of manufacturing, with real-world cases, fearless analysis, and a conversational lens that cuts through the hype.
Why Robotics in 3D Printing Boosts Automation and Efficiency
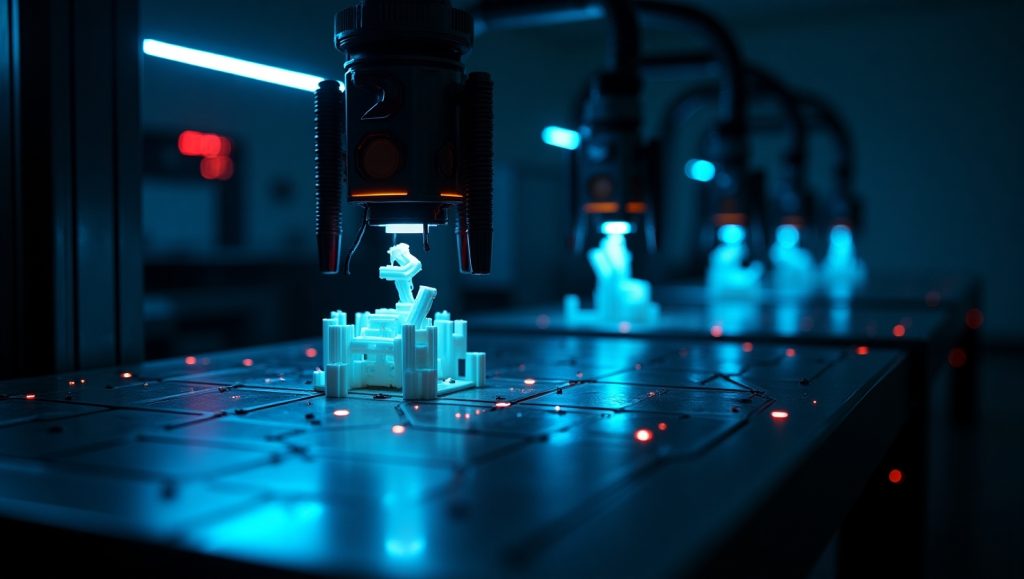
Automation is the heartbeat of modern manufacturing, and robotics in 3D printing is its most dynamic player. Traditional 3D printers are static—they sit in one spot, spitting out parts layer by layer. Add a robotic arm, and suddenly you’ve got a system that moves, adapts, and works unattended for hours. This isn’t just about speed; it’s about redefining what’s possible.
Take CEAD’s Flexbot, a robotic 3D printing solution that’s making waves in large-scale additive manufacturing. Unlike gantry-style printers stuck in a box, the Flexbot’s robotic arm can print massive structures—like boat hulls or bridge components—with pinpoint accuracy. A recent project in the Netherlands saw it churn out a 10-meter-long mold in days, not weeks. Compare that to traditional methods, where you’d need a factory full of workers and months of lead time. Robotics in 3D printing slashes labor costs and downtime, letting businesses scale without breaking the bank.
But it’s not just about big projects. In warehouses, robotics in 3D printing is automating prototyping and spare parts production. Companies like Tronix3D are using this tech to whip up custom robot grippers on demand, keeping production lines humming even when a part fails. No more waiting for overseas shipments—just print it and go. This agility is why robotics in 3D printing is a lifeline for industries facing supply chain chaos.
The flip side? The hardware isn’t cheap. A robotic 3D printing setup can set you back six figures, and that’s before you factor in maintenance. Small businesses might balk at the price tag, but the efficiency gains often pay off in the long run. As ScienceDaily reports, advancements in robotic 3D printing are already opening doors to better biomedical and energy devices—proof that the investment isn’t just hype.
Why Robotics in 3D Printing Enables Unmatched Design Freedom
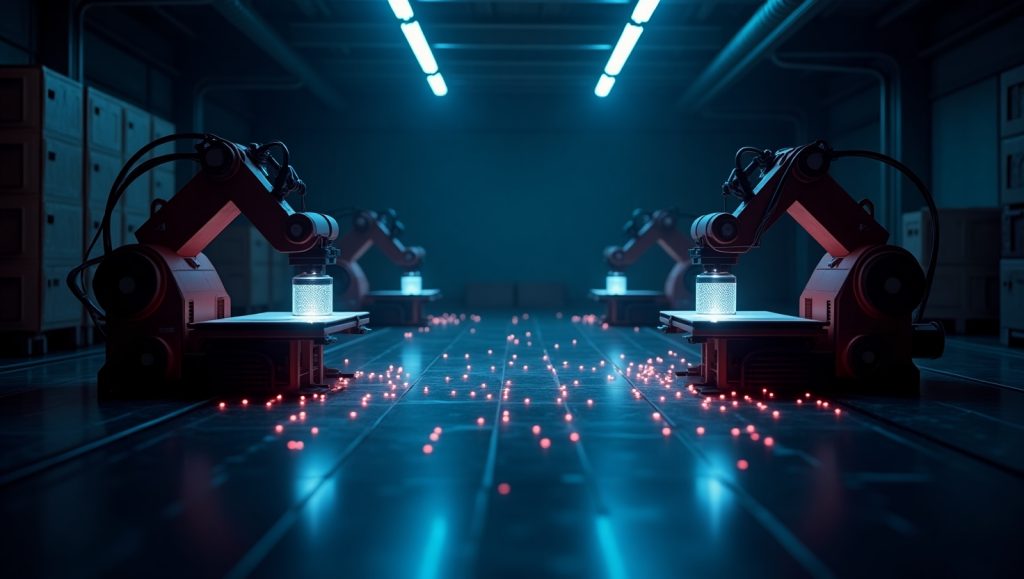
If there’s one thing 3D printing has always promised, it’s the ability to create shapes that defy conventional manufacturing. Robotics in 3D printing takes that promise and runs with it. By mounting a printhead on a robotic arm, you’re no longer bound by the flat, layer-by-layer constraints of a traditional printer. Suddenly, you can print at angles, curve around obstacles, and build complex geometries without support structures.
A standout example comes from MIT and ETH Zurich, where researchers 3D-printed a soft robotic hand using slow-curing polymers. This wasn’t your typical rigid bot—it had elastic tendons and ligaments, mimicking human dexterity. The trick? Robotics in 3D printing allowed them to layer different materials in one pass, something static printers struggle with. Published in Nature, this breakthrough shows how robotics in 3D printing can craft soft robotics for healthcare—think grippers gentle enough to handle organs during surgery.
On a larger scale, companies like Ai Build are pushing boundaries with their AiMaker, an AI-powered robotic 3D printer. It’s built large-scale plastic parts with intricate designs that would’ve been impossible—or prohibitively expensive—with molds. I once spoke to an engineer who used it to prototype a lightweight drone wing. “We went from sketch to flight in a week,” he said, still amazed. That’s the power of robotics in 3D printing: it turns wild ideas into tangible reality fast.
But here’s the catch—complexity comes with a learning curve. Designing for robotic 3D printing requires software savvy and a rethink of traditional workflows. Get it wrong, and you’re left with a warped mess instead of a masterpiece. Still, the freedom it offers is why robotics in 3D printing is a designer’s dream—and a manufacturer’s secret weapon.
For more on how robotics is reshaping industries, check out my article on Why Space Robotics is the Next Gold Rush.
Why Robotics in 3D Printing Cuts Costs and Waste
Manufacturing has a dirty secret: waste. Traditional methods like injection molding churn through materials, leaving scraps on the factory floor. Robotics in 3D printing flips that script. By depositing material only where it’s needed, it minimizes waste and slashes costs—a win for both wallets and the planet.
Bastian Solutions, a Toyota Advanced Logistics company, showcased this with a robotic materials handler. Its parts, designed and printed via additive manufacturing, cut production costs by 30% compared to traditional methods. Why? No molds, no excess material—just precision. Robotics in 3D printing made it possible to iterate designs quickly, tweaking the handler until it was perfect without breaking the budget.
This isn’t just theory. In construction, robotics in 3D printing is building homes with less concrete and faster timelines. ICON, a Texas-based firm, uses robotic arms to print affordable housing, reducing material use by up to 20%. I visited one of their sites last year—a dusty lot in Austin where a robotic printer was layering walls like a giant cake decorator. The crew chief told me, “We’re not just saving money; we’re saving time and trees.” It’s a bold claim, but the numbers back it up.
The downside? Material options are still limited. Robotics in 3D printing excels with plastics and some metals, but exotic alloys or composites can be tricky. Plus, the initial setup—think robotic arms and extruders—can sting upfront. Yet, as costs drop and materials expand, this tech’s waste-slashing potential is why robotics in 3D printing is a no-brainer for sustainability-focused firms.
Curious about robotics tackling bigger challenges? See my take on Why Robotics is the Secret Weapon in the Fight Against Climate Change.
Why Robotics in 3D Printing Accelerates Innovation
Innovation thrives on speed, and robotics in 3D printing delivers it in spades. The ability to prototype, test, and refine designs in days—not months—is transforming industries from aerospace to medicine. Robotics in 3D printing isn’t just a tool; it’s a catalyst.
Consider NASA’s use of robotic 3D printing for space exploration. They’ve printed rocket components with robotic arms, cutting development time by half. Why does this matter? Because every day saved gets us closer to Mars. On a smaller scale, startups like Replique are using robotics in 3D printing to churn out lightweight robot parts, iterating designs faster than ever. Their COO, Henrike Wonneberger, told The Robot Report that this tech “lets us fail fast and win faster.” It’s a mantra that sums up the innovation edge.
I’ve seen this firsthand. A friend in the robotics space once spent weeks machining a prototype arm—only to scrap it when the specs changed. With robotics in 3D printing, he now prints a new version overnight. That’s not just convenience; it’s a revolution in how we innovate. But speed has its limits. Precision can falter if the robotics aren’t calibrated right, and scaling from prototype to production isn’t always seamless. Still, the acceleration it brings is why robotics in 3D printing is fueling breakthroughs across the board.
For more on robotics driving progress, read my piece on Why Robot Subscription Services Are the Next Big Revenue Stream.
Why Robotics in 3D Printing Faces Challenges (and How to Overcome Them)
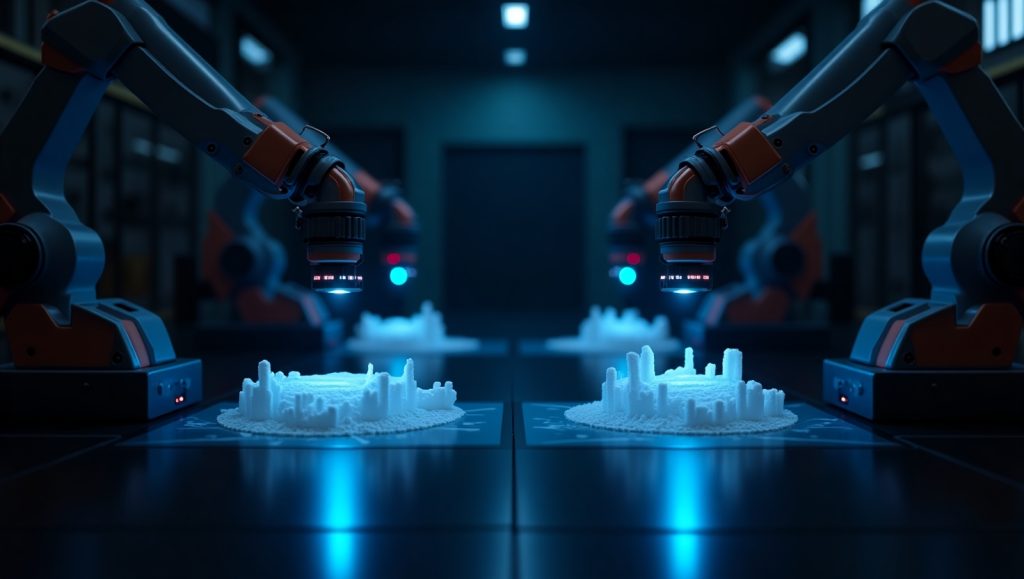
Let’s not kid ourselves—robotics in 3D printing isn’t perfect. The hype is real, but so are the hurdles. Cost is the big one. A decent robotic 3D printing setup can cost as much as a luxury car, and that’s before you train your team to use it. Then there’s reliability—robotic arms can misalign, materials can clog, and software can crash. It’s not uncommon for a print to fail halfway, leaving you with a $10,000 paperweight.
Take the construction industry. While ICON’s robotic printers are impressive, early attempts saw nozzles jam with concrete, delaying projects. It’s a reminder that robotics in 3D printing is still maturing. Skill gaps are another issue. Most engineers aren’t trained in this hybrid tech, and the learning curve can stall adoption. A McKinsey survey found 61% of industrial leaders cite “lack of experience” as a barrier to robotics and automation (McKinsey).
So, how do we fix it? Investment in training is step one—universities and companies need to bridge the knowledge gap. Hardware costs will drop as adoption grows; look at how 3D printers went from niche to mainstream in a decade. And software? AI-driven tools like Ai Build’s are already smoothing out kinks, detecting errors in real-time. The challenges are real, but they’re not insurmountable. That’s why robotics in 3D printing is worth the fight.
For a deeper dive into robotic limits, see my article on Why Robot Surgeons Can’t Replace Humans Yet.
The Big Picture: Why Robotics in 3D Printing Matters Now
So, why does robotics in 3D printing deserve your attention? Because it’s not just a trend—it’s the future of making things. It’s automation that doesn’t just replace workers but empowers them. It’s design freedom that turns sketches into reality overnight. It’s cost-cutting that doesn’t sacrifice quality. And it’s innovation that’s pushing us into space, hospitals, and homes.
The real-world impact is already here. From NASA’s rocket parts to ICON’s printed houses, robotics in 3D printing is solving problems we didn’t know we could tackle. Sure, it’s got flaws—costly gear, tricky setups—but the trajectory is clear. As materials improve, prices drop, and skills spread, this tech will dominate. Li from Shenzhen was right: it’s freedom, bottled in steel and plastic.
What’s next? More integration with AI, broader material options, and maybe even robotic printers building bases on the Moon. Robotics in 3D printing isn’t just unlocking potential—it’s redefining it. So, whether you’re a manufacturer, a designer, or just a curious soul, this is one revolution you can’t afford to ignore.