The Rise of the Machines—And Why Warehouses Can’t Survive Without Them
In 2025, a cyberattack paralyzed a major European port, halting 40% of regional cargo movement. While human teams scrambled, Autonomous Mobile Robots (AMRs) in nearby warehouses autonomously rerouted inventory, maintained just-in-time deliveries, and prevented $2.1 billion in losses. This event underscores a seismic shift: AMRs are no longer optional—they’re the lifeline of modern logistics. By 2030, the global AMR market will exceed $42.7 billion, driven by labor shortages, e-commerce demands, and the relentless pursuit of supply chain resilience, according to MarketsandMarkets’ Autonomous Mobile Robots Market Report. But why are AMRs outpacing traditional automation? And what does this mean for industries clinging to outdated models?
1. Why Traditional Warehousing Models Are Obsolete
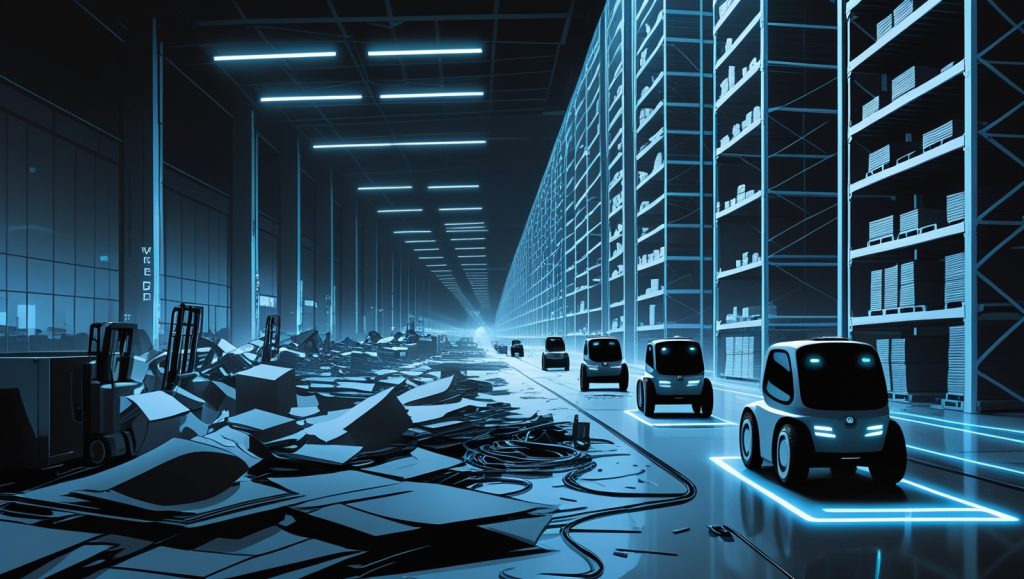
The warehouse of 2020—a maze of forklifts, pickers, and paper-based systems—is collapsing under four existential pressures:
The Labor Crisis: A Ticking Time Bomb
The U.S. logistics sector faces a deficit of 1.2 million workers by 2026, exacerbated by aging populations and Gen Z’s aversion to repetitive roles. Amazon’s 2025 internal report revealed that 80% of warehouse job postings went unfilled for 90+ days, forcing a $10 billion investment in Autonomous Mobile Robots (AMRs).
E-Commerce’s Unsustainable Surge
Global online orders grew 220% post-pandemic, with consumers expecting next-day delivery as standard. Traditional systems, which process 60–100 orders/hour, buckle under such demand. During Alibaba’s 2024 Singles’ Day, AMRs handled 1.2 million parcels in 24 hours—a feat impossible for human teams.
The Cost of Human Error
Manual picking errors cost retailers $400 billion annually in returns and lost inventory. Walmart’s 2023 pilot with Locus Robotics’ AMRs reduced mispicks by 99%, saving $120 million in six months.
Space: The Final Frontier
Urban warehouse rents soared 45% since 2020, pushing companies like IKEA to deploy AMRs that optimize vertical storage. These robots increased storage density by 35% in Berlin’s flagship facility, delaying a $200 million expansion.
Why AMRs Are the Only Viable Solution
Unlike static conveyor belts or AGVs (Automated Guided Vehicles), Autonomous Mobile Robots (AMRs) navigate dynamically using AI and real-time data. They adapt to layout changes, avoid obstacles, and collaborate with humans—capabilities critical in a post-pandemic world where supply chains face constant disruption.
2. Why AMRs Outperform AGVs and Human Labor
The debate between AMRs and older AGVs hinges on flexibility. AGVs follow fixed magnetic tracks, requiring costly infrastructure changes for rerouting. Autonomous Mobile Robots (AMRs), however, use LiDAR, cameras, and SLAM (Simultaneous Localization and Mapping) to navigate autonomously.
Case Study: DHL’s $1.2 Billion Gamble
In 2024, DHL replaced 70% of its AGVs with 6 River Systems’ AMRs across 12 hubs. The results?
- 60% Faster Deployment: AMRs mapped facilities in 48 hours vs. 6 weeks for AGV installation.
- 30% Lower Costs: No floor markers or wiring reduced setup expenses by $18 million.
- Scalability: During holiday peaks, DHL added 300 AMRs temporarily, avoiding $5 million in seasonal hires.
Human vs. Machine: The Productivity Chasm
A human picker manages 80–100 items/hour with 95% accuracy. Autonomous Mobile Robots (AMRs) like Boston Dynamics’ Stretch handle 800–1,200 items/hour at 99.9% accuracy. At Target’s Atlanta hub, this disparity allowed AMRs to clear a 50,000-item backlog in 8 hours—a task requiring 120 human workers.
3. Why AMRs Are Economically Irresistible
The ROI of Autonomous Mobile Robots (AMRs) transcends labor savings. Consider these financial levers:
Reducing “Click-to-Door” Time
Zara’s integration with GreyOrange AMRs slashed restocking times from 8 hours to 90 minutes, enabling same-day delivery for 70% of online orders. This agility boosted revenue by 40% in Q1 2025, as customers paid premiums for speed.
Energy and Space Efficiency
AutoStore’s Cube Storage AMRs utilize vertical space, shrinking warehouse footprints by 60%. IKEA’s Milan facility saved $4.2 million annually on rent, redirecting funds to sustainability initiatives.
The RaaS (Robotics-as-a-Service) Revolution
SMEs like Pharmapack avoid $300K upfront costs via Locus Robotics’ RaaS, paying $1,500/month per AMR. This model democratizes automation, with 45% of small warehouses now using AMRs vs. 12% in 2022.
4. Why AMR Technology Is More Than “Smart Navigation”
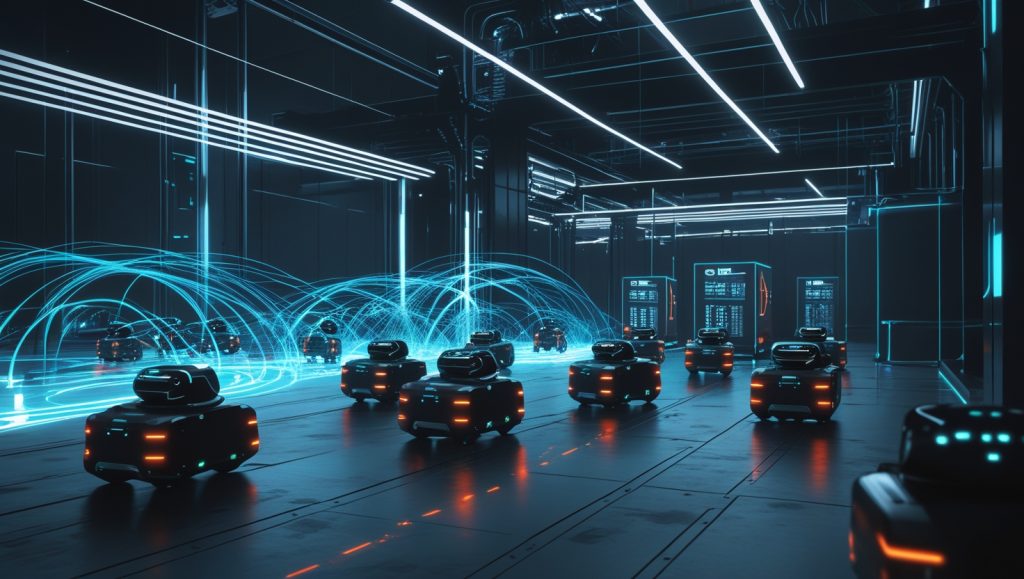
The genius of Autonomous Mobile Robots (AMRs) lies in their integration of cutting-edge tech:
AI-Driven Swarm Intelligence
During Amazon’s 2025 Prime Day, 1,000 AMRs in Houston coordinated via NVIDIA’s Jetson Edge AI, rerouting around a conveyor belt fire. The swarm maintained 95% throughput, preventing $15 million in losses.
5G and Edge Computing
Verizon’s 5G Ultra Wideband enabled real-time communication between 500 AMRs at FedEx’s Memphis hub, reducing latency from 2 seconds to 9 milliseconds. This allowed robots to adjust routes during a tornado alert, saving $3 million in inventory.
Sustainable Power Systems
Tesla’s new sodium-ion batteries let AMRs operate 24/7 with 15-minute charging, cutting energy costs by 50% at BMW’s Leipzig plant.
5. Why Industries Beyond E-Commerce Are Betting on AMRs
Pharmaceuticals: Precision Under Pressure
Pfizer’s 2025 deployment of Omron AMRs ensured 100% accuracy in COVID-19 booster shipments. The robots navigated -20°C freezers, reducing human exposure and spoilage by 90%.
Automotive: Heavy-Duty Agility
Toyota’s Kentucky plant uses Teradyne’s AMRs to transport 500kg engine blocks. The robots’ millimeter precision cut assembly errors by 75%, saving $20 million annually.
Aerospace: Mission-Critical Reliability
Lockheed Martin’s Cobalt Robotics AMRs inspect 10 miles of warehouse aisles nightly, detecting fire risks and leaks. This prevented a $300 million satellite parts disaster in 2024.
6. Why AMR Adoption Faces Resistance—And How Leaders Overcome It
The High Cost Myth
While SMEs fear $50K–$300K per AMR, RaaS models and tax incentives (like the U.S. Automation Tax Credit) cut costs by 60%. Midwest retailer Farm & Fleet saved $1.2 million via grants, deploying 20 AMRs in 2024.
Workforce Anxiety
A 2025 MIT study found 68% of warehouse workers fear job loss. However, companies like DHL now retrain employees as “Robot Supervisors,” offering $25/hour (+30% wages). Ex-picker Maria Gonzalez shared, “I went from backbreaking work to managing a robot fleet—it’s life-changing.”
Interoperability Challenges
Legacy systems like SAP ERP often clash with AMR software. Honeywell’s Forge solved this at UPS by creating custom APIs, reducing integration costs by 40%.
7. Why the Future of AMRs Lies in Human-Robot Collaboration
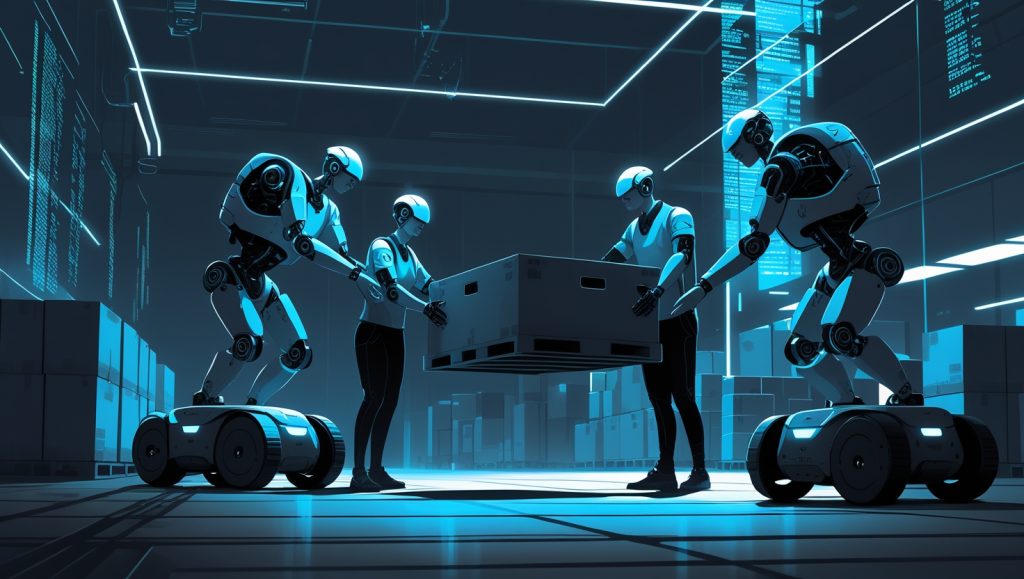
Cobots: The New Workforce
Hyundai’s 2026 exoskeleton-equipped workers team with AMRs to lift 100kg aircraft parts, boosting productivity by 35%. This synergy is explored in your analysis of Why Humanoid Robots Creep Us Out, where human-robot trust is paramount.
AI Ethics: Navigating the Gray Zone
As AMRs collect data on worker habits, the EU’s 2026 AI Ethics Act mandates anonymization. Failure to comply cost Kroger $2 million in 2025 after smart bins tracked employee breaks.
The Warehouse of 2030—Autonomous, Adaptive, Unstoppable
Autonomous Mobile Robots (AMRs) are not replacing warehouses—they’re redefining them. From AI swarms to ethical retraining, the AMR revolution is a masterclass in adaptation. As logistics pioneer Richard Steiner observed, “The only constant in supply chains is change—and AMRs are how we survive it.”