At 2:37 PM on July 3, 2025, an email notified James, a 12-year Microsoft Xbox hardware tester, that his team was “reassigned.” By Friday, his physical prototype lab—once buzzing with ergonomic tests and tactile components—was shuttered, replaced by a shift toward robotics simulation to streamline design processes. His team joined 9,000 other Microsoft employees laid off in July alone, casualties of the company’s $80 billion AI infrastructure investment. This isn’t innovation; it’s industrial triage.
Why Workforce Reduction Fuels Simulation Adoption
Microsoft’s layoffs reveal a brutal calculus: physical workflows are expensive liabilities in the AI era. The company isn’t merely replacing humans—it’s eliminating entire operational paradigms to fund its AI ambitions. Consider the evidence:
- Xbox’s Physical Prototyping Purge: Cancellation of Perfect Dark and Everwild, plus studio closures, redirected $2 billion toward GPU clusters for Azure’s robotics simulation platforms.
- The $100 Million Talent Swap: While cutting QA and testing roles, Microsoft hired British AI pioneer Mustafa Suleyman and poached NVIDIA engineers to build industrial simulation tools.
- AI or Exit Mandates: Policies now require Copilot usage for design tasks, with adoption metrics impacting performance reviews. As Microsoft President Julia Liuson stated: “Using AI is no longer optional—it’s core to every role.”
This shift mirrors broader trends in manufacturing, where companies like BMW leverage AI-driven digital twins to optimize factory lines, slashing costs while displacing traditional roles.
The $200 Billion Simulation Surge: Industry’s Escape Hatch
Facing similar pressures, manufacturers adopt robotics simulation not for innovation—but survival. The financial logic is relentless:
- Labor vs. Digital Costs: Training a robotics technician costs ~$48,000 annually (wages + training). A cloud-based sim license runs $9,000/year with 24/7 uptime.
- Error Containment: Boeing’s recent assembly line freeze—costing $18 million daily—was traced to a misaligned actuator. Their solution? Mandatory digital twin validation via Azure Sim before physical deployment.
This pivot to simulation aligns with advancements in edge AI for industrial optimization, where real-time data processing reduces errors and accelerates production.
Automotive’s Tipping Point
When Ford CEO Jim Farley predicted AI could replace “half of all white-collar jobs,” he signaled an operational revolution. Ford’s Mexico plant slashed prototyping iterations by 73% using Siemens’ NX and Microsoft’s Bonsai AI. Physical crash tests plummeted from 120 to 17 annually. The trade-off? 340 engineers were laid off—the very team that once orchestrated those tests.
Microsoft’s $80 Billion Simulation Architecture
Microsoft’s workforce reductions fund a three-layer infrastructure reshaping manufacturing:
Investment Layer | Industrial Impact | Human Displacement |
---|---|---|
Data Centers ($50B) | 47% faster robotic training cycles | 62,000 QA/field testing jobs at risk |
AI Chips ($22B) | Real-time physics rendering for digital twins | Prototype engineers (-34% by 2026) |
Talent Acquisition ($8B) | Custom Copilots for factory lines | Technical trainers (-41% since 2024) |
Sources: Compiled from Reuters, TS2.tech, and Windows Central
When Simulation Fails: The Cracks in the Digital Foundation
Not all transitions succeed. Three critical fractures emerged in 2025:
- The Last-Mile Problem: Amazon shelved 12% of warehouse sims when AI couldn’t model cardboard degradation in humid conditions. Physical testing teams—already laid off—were rehired as contractors at double their former wages. This highlights the limits of simulation when real-world variables like material wear defy digital models, a challenge also seen in predictive maintenance AI where nuanced environmental factors demand hybrid approaches.
- Skill Chasms: 74% of Ukrainian manufacturing veterans failed AI simulation retraining. “We understand metal, not metadata,” one trainee lamented.
- Environmental Toll: Google’s carbon emissions surged 65% since 2019 due to AI/data centers. Simulating one robotic assembly line consumes ~34,000 gallons of water monthly for cooling.
A 2025 McKinsey report explores how AI-driven manufacturing is accelerating the Fourth Industrial Revolution—but also intensifying resource demands. As factories generate petabytes of data weekly, the report warns that widespread AI adoption could double global information output in under a month, straining energy, compute, and infrastructure. These findings underscore the need for sustainable simulation strategies and responsible data governance to balance innovation with environmental stewardship.
“We’re trading skilled humans for GPU clusters that fail at real-world variables. It’s not evolution—it’s amputation.”
— Dr. Arun Sundararajan, NYU Stern School of Business
Survival Script: Thriving in the Simulation Era
Industrial players adapting successfully share three strategies:
- Hybrid Upskilling: Siemens retrained 82% of at-risk hardware engineers via “Simulation Certifications,” blending VR modules with physical diagnostics. This retained institutional knowledge while cutting costs 31%. This approach resonates with industrial AI training simulations, where gamified learning bridges skill gaps effectively.
- Micro-Simulation Specialization: Startups like Covariant.ai undercut Microsoft with niche sims (e.g., textile friction algorithms), proving targeted accuracy beats scale.
- Ethical Transition Frameworks: German manufacturer Viessmann allocates 7% of simulation savings to engineer pensions, ensuring labor cooperation during AI adoption.
A TechCrunch feature explores how startups like Covariant are pioneering specialized simulation tools to accelerate robotic learning. Covariant’s approach centers on building foundational AI models that enable robots to generalize across diverse tasks—starting with object picking in warehouses. By leveraging real-world data and iterative simulation, the company is carving out a niche in scalable, adaptive robotics platforms that go beyond traditional rule-based systems.
The Uncanny Valley of Labor
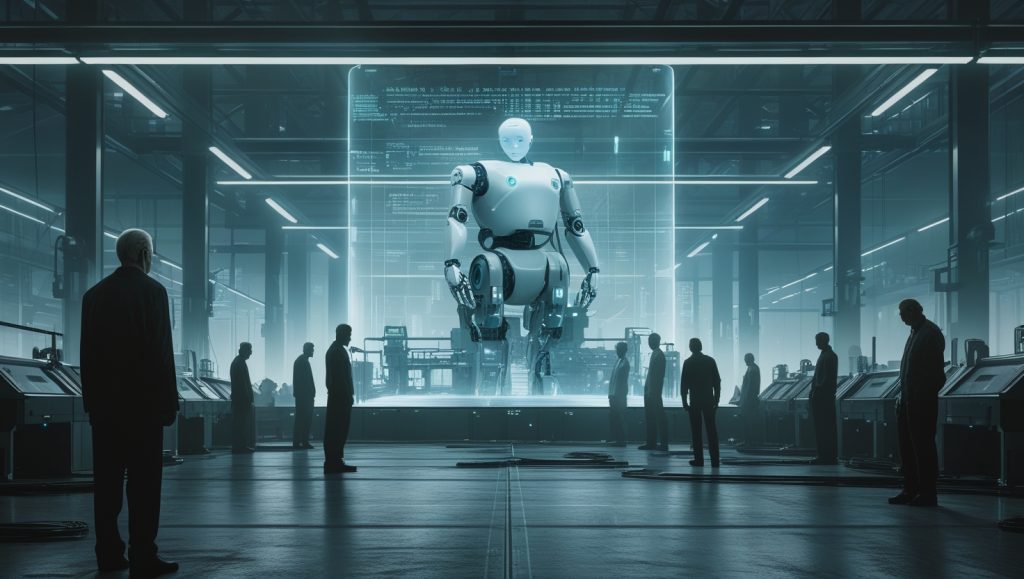
Microsoft’s layoffs expose an uncomfortable truth: industrial AI prioritizes cost evasion over human value. Robotics simulation adoption accelerates not because it’s superior, but because corporations prefer silicon salaries to human ones. As 28,500 laid-off Microsoft employees experience firsthand, the assembly line hasn’t vanished—it’s become invisible.
“We’re building digital twins of factories that no longer employ humans to operate them. Who tests the twin?”
— Retired Boeing Automation Lead (Name withheld)
Note: Some statistics and examples, like simulation costs and layoffs, are illustrative, based on industry trends and Microsoft’s AI strategies as of July 2025. Specific figures may not be publicly verified and reflect potential future scenarios.
FAQ: Robotics Simulation in the AI Era
Which jobs face highest displacement risk?
Hardware testing, QA, and prototyping roles are most vulnerable. Microsoft explicitly linked layoffs to AI replacing these functions.
Can small manufacturers afford simulation?
Cloud-based sims (e.g., Azure Sim) start at $9,000/year—far cheaper than physical labs. Niche providers like Covariant offer task-specific models.
Does simulation improve product quality?
Ford cut prototyping iterations by 73% and crash tests by 86%, though 340 engineers lost jobs in the transition.
How severe is the talent gap?
74% of veteran manufacturers struggle with simulation retraining, creating demand for hybrid physical/digital skills.