The 44% Problem: When Sensors Cry Wolf
The promise was seductive: AI-driven factories humming with predictive precision. Yet on the plant floor, a silent rebellion brews. Recent data from Gartner reveals a staggering pain point: 44% of factory-floor sensors contribute to industrial AI false positives, triggering alerts for faults that don’t exist. These phantom warnings flood control rooms, erode trust in AI, and force operations teams into covert triage mode.
Why does this matter? Every false alarm isn’t just noise. It’s delayed shipments, wasted technician hours, and eroded confidence in digital transformation. When a temperature sensor falsely flags overheating on a critical CNC machine, ops teams scramble. Production halts. Engineers rip apart components. Only to find… nothing. The cost? One automotive supplier tracked $2.1M in annual losses from unnecessary downtime triggered by false alerts. For a deeper dive into how AI can still drive efficiency despite these challenges, see how industrial AI implementation wins big in 2025 factories.
Why Sensors Betray AI: The Root Causes
1. Sensor Drift & Environmental Warfare
Sensors live brutal lives. Vibration, dust, temperature swings, and electromagnetic interference batter them relentlessly. A voltage sensor near a welding station might misfire due to power surges. A pressure gauge in a humid environment drifts out of calibration. As Dr. Elena Rossi, MIT Industrial IoT Lab Lead, states: Most factory sensors endure conditions far beyond lab specs. Without constant recalibration, their data becomes poetic fiction. To explore how advanced sensors are addressing these issues, check out top 7 industrial IoT platforms for smart factories.
2. AI’s Brittle Training Data
AI models train on “clean” historical data, but real-world chaos is absent. If an AI never saw data from a sensor caked in oil sludge, it misreads signal noise as a bearing failure. Forbes reports that 78% of industrial AI projects use inadequately diverse training sets, creating blind spots. This problem echoes broader AI training challenges, as seen in why AI in robotics is failing, which unpacks the limits of current AI models.
3. Integration Silos & Context Blindness
A vibration spike on Conveyor B might be catastrophic—or just a forklift rumbling past. Most AI systems lack cross-system context. Sensor data gets analyzed in isolation, divorced from adjacent processes. As one plant manager told me (anonymized): Our AI saw a thermal spike on Machine 7 as ‘overheating.’ It didn’t know we’d just switched to a high-friction material. For insights into how integrated systems can solve this, learn about edge AI vs. cloud AI for industrial optimization.
The Ops Team Playbook: Quiet Overrides in Action
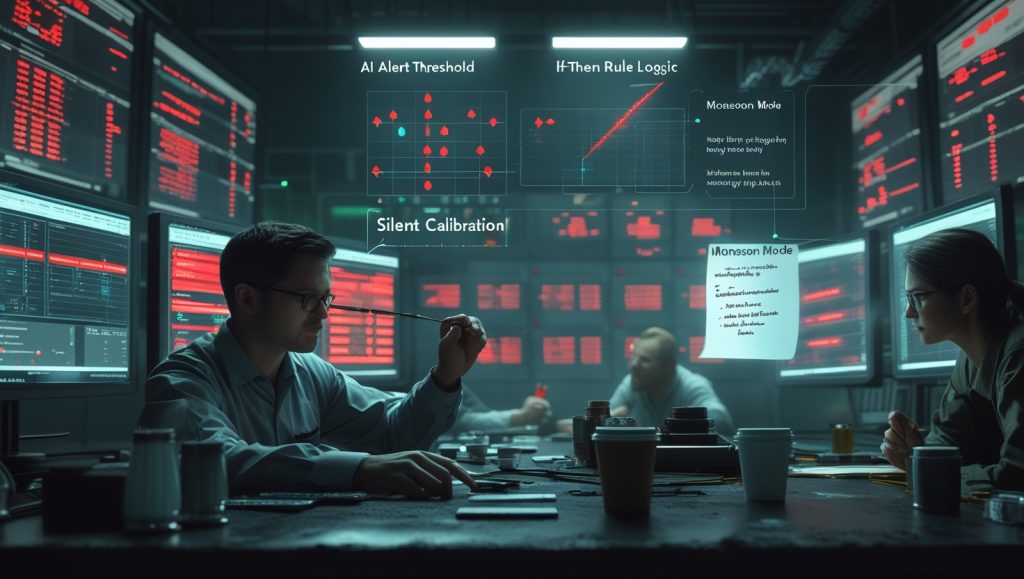
Faced with screaming dashboards of false red alerts, operations teams deploy guerrilla tactics to keep lines running:
Tactic 1: Threshold Tweaking (The “Silent Calibration”)
Instead of waiting for IT, ops engineers manually adjust AI alert thresholds. If an AI flags bearing vibrations above 6.2mm/s, but historical data shows false alarms below 7.5mm/s, they nudge the limit. “We call it ‘AI whisperer work,’” says Marcus Chen, a veteran automation engineer. “The system stays live, but we filter the noise.”
Tactic 2: Rule-Based Overlay Systems
Teams layer simple “if-then” rules atop AI outputs:
- IF vibration alert fires on Pump A
- AND pressure on Line B is stable
- AND no upstream maintenance in last 2 hours
- THEN flag as ‘low priority’
This hybrid approach cuts false alerts by up to 63%, per Deloitte’s 2024 Smart Factory Survey. To see how such systems enhance reliability, discover why unsupervised anomaly detection saves factories in 2025.
Tactic 3: Tribal Knowledge Logs
When Maria Rodriguez (name changed), a shift supervisor at a chemical plant, noticed moisture sensors falsely triggering during monsoon season, her team created a manual “monsoon mode” log. Now, when humidity exceeds 80%, alerts require secondary validation. “AI doesn’t know monsoons,” she shrugs. “We do.”
Fixing the Foundation: Beyond Quick Fixes
While ops teams bandage the bleeding, strategic solutions are emerging:
1. Self-Diagnosing Sensors
Companies like Siemens and Rockwell Automation now embed self-health checks in sensors. Devices monitor their own drift, temperature tolerance, and signal integrity—flagging when their data is unreliable. As Rockwell’s CTO, Brian Shepherd, states: A sensor should report on itself before reporting on machines. For more on cutting-edge sensor advancements, Siemens’ innovations in smart sensor technology are setting new standards
2. Context-Aware AI Architectures
Next-gen systems like Sight Machine’s PlantLens ingest data from adjacent systems (MES, ERP, weather APIs). If a thermal alert fires during a planned material changeover, the AI cross-references work orders before escalating.
3. Human-in-the-Loop Validation
Platforms like Augury combine AI diagnostics with human expert review. Suspicious alerts route to engineers who confirm/deny faults—feeding results back to retrain the AI. This closed loop slashes false positives by 41% in 6 months. To understand how human-AI collaboration is transforming industries, IBM’s AI-driven manufacturing solutions offer a scalable model (do-follow link).
The Cost of Ignoring Industrial AI False Positives
The stakes transcend annoyance. Unchecked false alarms cause:
- Alert fatigue: Critical warnings drown in noise.
- Unplanned downtime: “Just in case” shutdowns cost manufacturers $50B annually (McKinsey).
- AI abandonment: Teams revert to manual checks, stalling Industry 4.0 progress.
The Path Forward: Trust Through Transparency
Industrial AI’s potential remains immense—but only if we address the credibility crisis. As Dr. Anil Varma, Head of AI at GE Digital, warns: Teams overriding alerts aren’t ‘cheating.’ They’re compensating for AI’s immaturity. The solution isn’t less human input—it’s AI that learns from it.
3 Immediate Actions for Manufacturers:
- Audit sensor health monthly—not yearly.
- Integrate contextual data (maintenance logs, shift reports) into AI models.
- Empower ops teams to flag false positives—and use that data to retrain AI.
Final Word: The Silent War for Reliability
That 44% false positive rate isn’t a tech failure—it’s a wake-up call. Industrial AI must evolve from isolated algorithms to integrated, self-aware systems. Until then, the unsung heroes of the factory floor will keep bridging the gap between AI’s promise and its delivery—one quiet override at a time.