The Warehouse That Maps Itself
On the outskirts of Tokyo, a fleet of autonomous robots navigates densely packed inventory aisles with millimeter precision. What makes this remarkable isn’t their movement—it’s that these machines constructed their own navigation maps during operations, adapting overnight to reconfigured storage zones without human intervention. This is SLAM for autonomous navigation in action—the unseen engine transforming industrial intelligence. For a deeper dive into how AI-driven automation is reshaping industries, explore how industrial AI agents slash energy costs in manufacturing in 2025.
Solving Robotics’ Impossible Puzzle
Simultaneous Localization and Mapping (SLAM) resolves a fundamental paradox: Robots can’t map environments without knowing their location, yet can’t locate themselves without a map. Dr. Sarah Lee, a robotics researcher, explains: “SLAM shatters this deadlock through probabilistic modeling and multi-sensor fusion.” Unlike GPS-dependent systems, SLAM-enabled robots generate real-time spatial understanding using:
- LiDAR sensors emitting 300,000 laser pulses/second to measure spatial geometry
- Visual odometry analyzing camera footage for feature tracking (e.g., ORB-SLAM detecting distinctive patterns)
- Inertial Measurement Units (IMUs) correcting motion drift during rapid turns
Table: Sensor Technologies Powering Industrial SLAM
Sensor Type | Accuracy | Optimal Use Cases | Key Limitations |
---|---|---|---|
LiDAR | ±2 cm | Low-light warehouses, precision tasks | High cost; struggles with reflective surfaces |
Visual SLAM (vSLAM) | ±5 cm | Dynamic environments; object recognition | Lighting-dependent; higher computational load |
Ultrasonic | ±10 cm | Ground-level obstacle detection | Limited range; ambient noise interference |
This fusion of sensors is critical for applications like industrial IoT platforms powering smart factories, where real-time data from multiple inputs drives efficiency.
Industrial Transformation Through Spatial Intelligence
The SLAM robotics market is projected to grow at 25.5% CAGR through 2032, fueled by logistics automation demands. Real-world implementations reveal tangible impacts:
Logistics Reinvented
Interlake Mecalux’s autonomous mobile robots reduced retrieval times by 40% in Spanish warehouses by combining LiDAR SLAM with dynamic path planning. Their systems update facility maps hourly, adapting to pallet movement without reprogramming. For insights into how similar automation boosts warehouse efficiency, check out how cobots maximize ROI in warehouses.
Manufacturing Resilience
At Bosch Rexroth factories, SLAM-guided cobots work alongside humans on assembly lines. Advanced algorithms distinguish between static machinery and moving workers, reducing collision incidents by 92%. This mirrors advancements in predictive maintenance AI leading factory efficiency in 2025, where proactive systems prevent costly downtimes.
Agricultural Precision
John Deere’s autonomous tractors employ multi-sensor SLAM to navigate uneven terrain while mapping soil compaction data—tasks impossible with pre-programmed routes. To understand how robotics extends to other innovative applications, read about robotic pollination solutions tackling the bee decline crisis.
Conquering Real-World Chaos
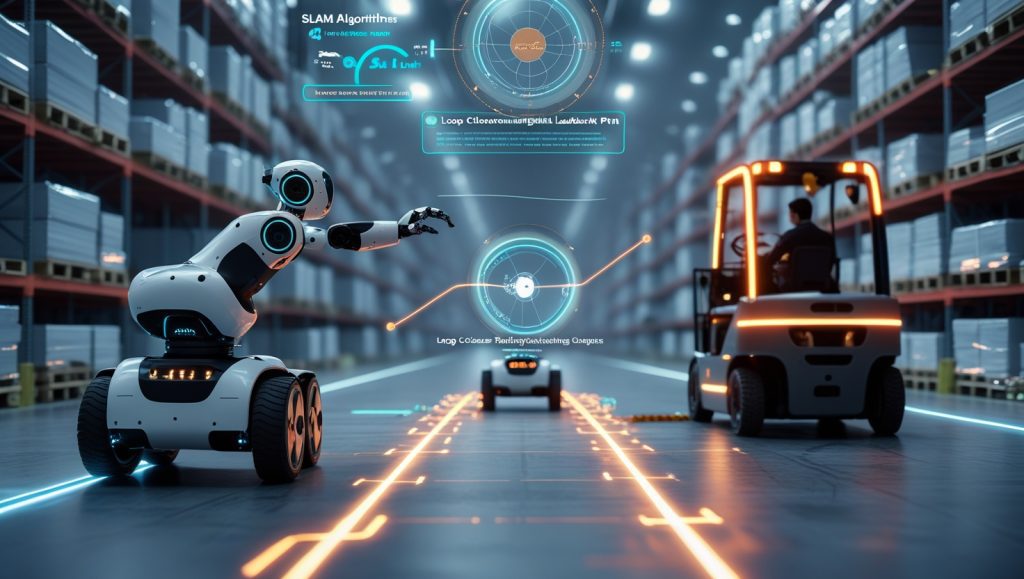
Industrial environments present extreme challenges that test SLAM’s limits:
The “Featureless Corridor” Dilemma
In vast warehouses with repeating rack structures, robots lose visual tracking references. Solutions like Google’s Cartographer SLAM use loop closure mechanisms. When robots recognize previously passed locations, they correct cumulative mapping errors—similar to hikers using landmarks for orientation. For more on how AI tackles complex industrial challenges, see this article on aerial manipulation systems.
Dynamic Obstacle Negotiation
Early SLAM assumed static environments. Modern systems like Mask R-CNN integrated SLAM identify moving objects (forklifts, workers) through a three-step process:
- Cameras detect human forms
- LiDAR confirms trajectory
- Path planners reroute within 500ms
This dynamic adaptability is crucial in fast-paced settings, as explained by experts at Robotics and Automation News, where SLAM’s role in logistics is transforming supply chains.
Case Study: Audi’s Warehouse Solution
After autonomous guided vehicles (AGVs) repeatedly stalled near reflective safety signage, engineers implemented polarized LiDAR filters and thermal cameras to distinguish real obstacles from glare. System downtime dropped 78%. This kind of innovation aligns with advancements in robotics simulation replacing physical prototyping, reducing costs and accelerating deployment.
The AI Inflection Point
Deep learning integration is overcoming historical SLAM limitations:
- Semantic SLAM classifies objects (“forklift,” “emergency exit”) rather than just mapping shapes. Neural networks trained on industrial imagery enable robots to understand what they navigate around.
- Predictive Pathing at Robotnik’s testing facilities shows robots anticipating human movement patterns using long short-term memory (LSTM) networks, reducing emergency stops by 60%.
- Cloud-Based Collaborative Mapping enables fleet learning. As a KUKA systems engineer notes: “One robot’s map becomes every robot’s map. Our systems share environmental updates like a hive mind for spatial awareness.”
Emerging Frontiers in Spatial Intelligence
- Swarm Coordination: Amazon’s upcoming drone fleets will collaboratively map 3D spaces, assigning tasks based on real-time positioning (e.g., high-level inventory checks vs floor transport).
- Edge Computing Integration: Processing SLAM algorithms locally via onboard GPUs cuts latency to <15ms—critical for high-speed manufacturing lines.
- Quantum SLAM: Early MIT research uses quantum annealing to solve large-scale mapping optimizations 200x faster than classical computers.
For a broader look at how quantum technologies are shaping robotics, visit Quantum Computing Report.
The Strategic Imperative
Companies delaying SLAM adoption face measurable disadvantages:
- Labor Efficiency Gap: SLAM-enabled autonomous mobile robots move 3x more goods/hour than human-operated forklifts.
- Reconfiguration Costs: Traditional AGVs require floor markings reinstalled during layout changes—costing $18,000/overhaul for mid-sized facilities. SLAM systems adapt autonomously.
As BlueBotics CEO Nic Mortinger observes, “We’ve passed the adoption tipping point. Facilities without adaptive automation will struggle to compete on flexibility or scalability.”
Frequently Asked Questions
How expensive is SLAM implementation?
Costs vary by system complexity. Basic LiDAR SLAM starts around $8,000 per vehicle, while multi-sensor industrial systems can exceed $45,000. However, ROI typically occurs within 14 months through reduced labor and downtime costs.
Can SLAM function without visible features?
Yes. Advanced systems use multi-modal sensor fusion combining LiDAR, inertial sensing, and wheel odometry. Underground mining equipment often operates in near-featureless tunnels using this approach.
How accurate is modern SLAM?
Industrial-grade systems achieve ±2 cm accuracy in optimized environments. Environmental factors like reflective surfaces or moving objects can reduce precision to ±15 cm, necessitating sensor fusion techniques.
What skills are needed to manage SLAM systems?
Implementation requires mechatronics engineers, AI specialists, and technicians trained in sensor calibration. PwC’s 2025 AI Jobs Barometer shows workers with these skills command 56% wage premiums.
How long does deployment typically take?
Pilot installations require 2-4 weeks. Enterprise-wide rollouts take 6-18 months, depending on facility size and legacy infrastructure integration needs.