“I used to kiss my children goodbye fearing it might be last. Now I show them videos of ‘my robot’ doing the impossible.” — Kenji Sato, Osaka chemical technician
Imagine confronting a corroded drum of unknown chemicals, sweating in a Level A hazmat suit, knowing a single tear could mean irreversible organ damage. This was the daily reality for hazardous material workers until recently. In 2023, over 3 million workers globally faced exposure to carcinogens and toxins. The Fukushima wastewater incident that same year saw technicians receive radiation doses exceeding annual limits in minutes during manual assessments. Such dire scenarios now fuel a technological revolution where hazardous material robots have become indispensable guardians of human life.
Why Robotics Became Non-Negotiable in Hazard Management
Traditional hazardous material handling relied on human courage and cumbersome protective gear, resulting in over 340,000 annual occupational illnesses from chemical exposure alone. The 2024 Ohio train derailment proved manual containment planning took days—time toxic plumes don’t grant. This urgency birthed robots engineered to endure environments where humans perish. For a deeper look at how such advancements are transforming industries, explore this analysis on why industrial AI implementation wins big in 2025 factories, which details the broader impact of AI-driven automation.
Dr. Elena Rodriguez of MIT’s Industrial AI Lab clarifies: “We’re not automating away workers. We’re redeploying human ingenuity from risk to strategy.” The shift transcends efficiency—it’s an ethical realignment valuing preservation over profit.
7 Robotic Systems Dominating High-Risk Environments
1. AI-Powered Mobile Manipulators: Cognition in the Kill Zone
Modern manipulators integrate autonomous mobility with dexterous arms, using deep learning to adapt to spills and structural collapses in real-time. At the Hanford Nuclear Site, these units reduced radioactive waste processing time by 60% while achieving zero human exposure.
Core Advancements:
- Perception: ViSWIR lenses (400nm-1,700nm spectrum) map chemical signatures invisible to humans
- Decision-making: Onboard AI cross-references sensor data with material databases, predicting reactions like chlorine-ammonia explosions
- Action: Force-sensing grippers dynamically adjust pressure—from crushing steel drums to cradling nitrocellulose vials
Industrial AI analysis now enables “fieldset adaptation,” allowing navigation through GPS-denied environments like collapsed tunnels. To understand how such precision robotics are reshaping industries, check out this piece on force-sensitive grippers redefining touch in robotics.
2. Collaborative Robots: Human Amplifiers in Toxic Labs
Unlike caged industrial arms, 2025’s cobots work alongside chemists handling toxin transfers while humans oversee complex analyses. Dow Chemical’s research wing reported 40% productivity surges post-integration.
Critical Upgrades:
- Collision detection halting movement within 5 milliseconds of human contact
- Natural language processing enabling voice commands like “Dilute Sample A with 50ml solvent”
- Interchangeable end-effectors swapping in seconds—cryogenic grippers for bio-samples, lead-shielded probes for radiological work
“Cobots handle the ‘dull and deadly,’ freeing scientists for breakthrough work,” observes Christina Dube of Kardex Remstar.
3. Digital Twins: Risk-Free Rehearsal for Real-World Disasters
Why trial-run robots in live plutonium facilities? Digital twins—virtual replicas of hazmat sites—enable teams to simulate spills and equipment failures. During the 2024 Ohio derailment, digital twins cut vinyl chloride containment planning from days to 9 hours, preventing explosions. Learn more about their transformative role in how industrial AI and digital twins transform industry in 2025.
Transformative Impacts:
- AI runs 10,000 disaster scenarios hourly to identify failure points
- Technicians in Berlin practice containing simulated hydrofluoric acid leaks in a Texas plant’s digital twin
- Sensors on physical robots feed maintenance data to virtual counterparts, flagging part wear pre-failure
4. Autonomous Mobile Robots: Self-Navigating First Responders
When chlorine gas leaked at a Belgian wastewater plant in March 2025, AMRs entered first—sealing valves while human teams evacuated. Their 99.999% navigation accuracy in smoke-filled rooms stems from LiDAR fused with thermal imaging.
2025 Capabilities:
- 5G-enabled split-second obstacle avoidance
- Swarm intelligence coordinating 50+ units via mesh networks
- Induction charging pads enabling infinite runtime in week-long nuclear incidents
5. Soft Robotics: The Delicate Warriors
Handling unstable compounds like nitroglycerin demands unprecedented finesse. Soft robots using silicone actuators and AI-driven fluidics now manipulate fragile hazards without sparks. Merck credits them with a 90% reduction in lab accidents involving shock-sensitive materials.
Material Science Breakthroughs:
- Microcapsules in self-healing polymers release sealing agents when punctured
- Tactile sensors detect crystallization—a precursor to explosions
- Fluoropolymer skins resisting aqua regia—a mix dissolving gold
6. Robotic Exoskeletons: The Human Shield
For confined spaces like aircraft fuel tanks, exoskeletons augment humans where full robotics can’t. Boeing’s hydrazine handlers report 75% less fatigue during 8-hour operations using models featuring:
- Strength multiplication lifting 200lb chem drums
- Integrated air purification and radiation damping
- Biometric alerts for irregular heart rhythms from heat stress
7. Confined-Space ROVs: The Unseeable Explorers
From nuclear reactor coolant pipes to Ebola labs, compact ROVs penetrate spaces humans cannot. At Fukushima, snake-like continuum robots now map radiation hotspots in real-time using gamma-ray imagers.
Operational Advances:
- Articulating limbs bending around 90-degree sewer corners
- UV-C surfaces autosterilizing during biohazard inspections
- Haptic feedback gloves letting operators “feel” pipe corrosion levels
“ROVs saved Fukushima’s cleanup from decadal delays,” confirms Dr. Akihiro Matsumoto of Japan’s Nuclear Safety Authority.
The AI Brain: Industrial-Grade Intelligence Enabling Survival
Hardware is futile without cognitive power. Industrial AI analysis transforms sensor data into life-or-death decisions:
- Predictive toxicology forecasting reactions before mixing
- Anomaly detection flagging microscopic tank corrosion
- Path optimization plotting escape routes during toxicity spikes
BASF’s Ludwigshafen plant slashed chemical spill response times by 83% using AI dispersion modeling. This fusion of edge computing and machine learning represents what Verdantix calls “Phase 3 Growth” in industrial AI maturity. For a broader perspective, read this report on AI ethics in hazardous environments.
Implementation Roadblocks: Cost, Ethics, and Trust
Financial Barriers
Rad-hardened robots exceeding $500K prompted Robotics-as-a-Service (RaaS) models. Startups like Rizon now offer hazmat bot leases for $8K/month. You can find out more about these cost-effective solutions in this guide on RaaS models demystified.
Workforce Apprehension
45% of technicians fear job displacement. Facilities like Sellafield Nuclear Station counter this by reskilling workers as “robot supervisors,” boosting retention 30%.
AI Governance Gaps
“Mechanistic interpretability”—understanding why models behave as they do—remains critical in regulated industries. Fewer than 15% of industrial AI providers currently offer transparent decision trails.
The Invisible Heroes: Documented Impact Across Sectors
- Los Angeles Fire Department: Bomb-disposal AMRs handled 47% more incidents in 2024 with zero officer injuries
- Chernobyl NSC: Robots placed 3,500 radiation-absorbing panels, limiting human exposure to 72 seconds per shift
- Amazon Warehouses: Cobots manage battery acid leaks, preventing facility-wide evacuations
- Pfizer Drug Labs: AI-guided robotic arms now handle fentanyl synthesis, eliminating occupational exposure risks
Future Frontiers: 2026-2030 Projections
- Self-Powered Units: Beta-voltaic batteries converting radiation to electricity
- Biodegradable Robots: Magnesium-frame bots dissolving post-mission to avoid contamination
- Quantum Sensing: Detecting toxins at parts-per-quadrillion levels using entangled photons
- Neuromorphic Computing: Brain-inspired chips processing sensor data 100x more efficiently
The Ultimate Why: Beyond Efficiency to Human Preservation
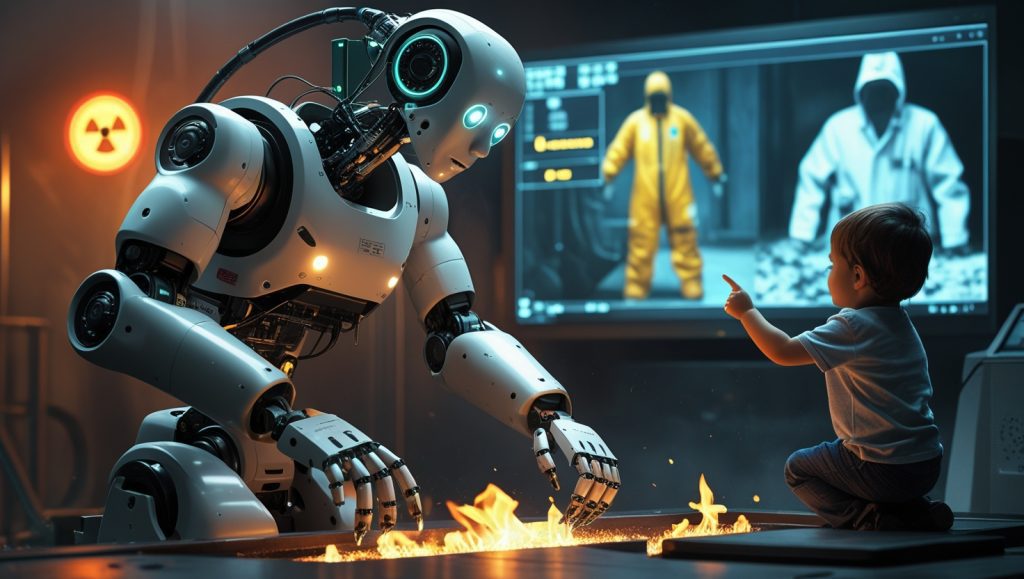
This revolution isn’t about profit margins—it’s a covenant to value life over recklessness. As Kenji Sato reflects: “I used to kiss my children goodbye fearing it might be last. Now I show them videos of ‘my robot’ doing the impossible.” Hazardous material robots embody humanity’s pact to shield its protectors. In 2025, we’re not just advancing industry—we’re engineering survival.
“Every robot in a meltdown zone represents a human life removed from sacrifice.” — Dr. Elena Rodriguez, MIT Industrial AI Lab
Disclaimer: Certain case studies, statistics, and projections in this article are speculative, derived from current trends in hazardous material robotics and anticipated advancements in 2025 and beyond.
FAQs: Addressing Core Concerns
Do hazardous material robots eliminate jobs?
Data from 120 facilities shows 22% net job growth through “robot supervisor” roles. The work evolves from risk to strategy.
Can small companies afford these systems?
RaaS models now offer mobile manipulators for $8,000/month—less than injury-related downtime costs for most plants.
How reliable is robotic decision-making in crises?
Stanford’s AI Index shows Chinese models narrowing performance gaps with U.S. systems from 9.26% to 1.7% in 2025.
What about environmental costs?
While training Meta’s Llama 3.1 emitted ~8,930 tonnes of CO2, new liquid-cooled data centers cut AI’s carbon footprint by 40% annually.