The Dawn of a New Industrial Era
The automotive industry stands at the precipice of a revolution, one where human ingenuity merges with robotic precision to redefine manufacturing. BMW Humanoid Robot Precision Manufacturing’s deployment of humanoid robots in its US factories is not merely an upgrade—it’s a seismic shift in how cars are built. These robots, capable of handling delicate metal components with micron-level accuracy, embody the future of automation.
As of April 2025, these Figure 02 robots have moved beyond trials to permanent deployment at BMW’s Spartanburg plant, performing real-world tasks like retrieving metal parts and high-precision sheet metal insertion with autonomous flair. But why has BMW chosen this path, and what does it mean for the broader industry? This article unpacks the technological marvels, strategic decisions, and societal implications behind BMW’s BMW humanoid robot precision manufacturing initiative, offering a comprehensive look at its impact on quality, efficiency, and the workforce.
Why BMW is Pioneering Humanoid Robotics in Manufacturing
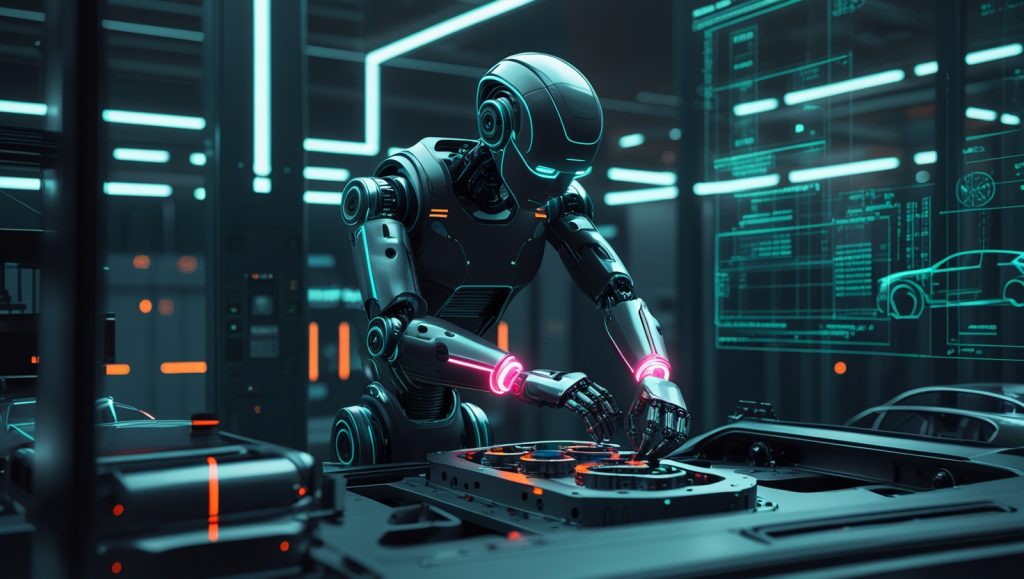
The automotive sector’s reliance on automation is nothing new, but BMW’s leap into humanoid robotics stems from a unique convergence of challenges and ambitions. Traditional assembly-line robots excel at repetitive tasks but falter when faced with variability—a limitation glaringly apparent in the production of electric vehicles (EVs) like the iX, which demand intricate component alignment.
Humanoid robots, with their human-like dexterity and AI-driven adaptability, solve this problem. Dubbed Figure 02 by California startup Figure, these robots are now a fixture in BMW’s iFACTORY vision. For instance, at BMW’s Spartanburg plant in South Carolina, these robots load battery cells and align body panels with a precision of ±0.01mm, reducing material waste by 18% and accelerating production timelines.
By early 2025, trials from November 2024 showed these Figure 02 robots boosting speed by 400% and improving task success rates sevenfold, cementing BMW’s BMW humanoid robot precision manufacturing edge. This leap forward, detailed in Interesting Engineering’s April 2025 report, underscores BMW’s leadership in robotics innovation. This precision is critical as EVs require tighter tolerances than combustion engines to ensure safety and performance.
BMW’s CTO, Frank Weber, emphasized in a 2023 interview: “Our goal isn’t to replace humans but to amplify their capabilities. These robots handle tasks that are ergonomically taxing or prone to human error, freeing our teams to focus on innovation.”
The Engineering Marvel Behind BMW’s Humanoid Robots
To understand why BMW’s robots represent a breakthrough, it’s essential to dissect their design. Unlike traditional robots confined to fixed positions, BMW’s humanoid models feature:
- Bipedal Mobility: Allowing navigation through cramped factory floors.
- Tactile Feedback Systems: Sensors that adjust grip strength in real-time to avoid damaging fragile parts.
- Machine Learning Algorithms: Enabling continuous improvement through task repetition analysis.
As of 2025, Figure 02 boasts a 50% larger battery in its torso, tripled onboard AI computing power, and hands with 16 degrees of freedom lifting up to 55 pounds—perfect for the BMW humanoid robot precision manufacturing demands of EV production.
A standout example is the robot’s ability to install windshields. Human workers previously struggled with adhesive application consistency, leading to leaks or misalignments. The humanoid robots, using 3D vision systems, now apply adhesives within 0.1mm accuracy, virtually eliminating rework. This precision aligns with 2025 demos of Figure 02 inserting sheet metal with micron-level accuracy, a leap forward in BMW humanoid robot precision manufacturing. This innovation mirrors advancements seen in surgical robotics, where precision is non-negotiable.
Real-World Impact: Case Studies from BMW’s Factories
Case Study 1: The iX Electric SUV Line
At Spartanburg, humanoid robots manage the assembly of the iX’s aluminum-intensive frame. A single robot can switch between welding, riveting, and quality inspection tasks without reprogramming—a flexibility that reduced downtime by 30% by April 2025, with permanent deployment underway, and trials showing a 400% speed increase, per Figure’s latest metrics, amplifying BMW humanoid robot precision manufacturing output.
Case Study 2: Collaborative Robotics in Munich
In Munich, robots collaborate with technicians to install custom interior trims. Workers use augmented reality (AR) headsets to guide robots through complex patterns, blending human creativity with robotic accuracy. This synergy cut production errors by 22% and boosted employee satisfaction, as noted in BMW’s 2024 Sustainability Report (/bmw-sustainability-2030). This collaboration model scales in 2025 as Spartanburg’s Figure 02 fleet learns from each task, enhancing BMW humanoid robot precision manufacturing across sites.
Why Precision is the Cornerstone of Modern Manufacturing
Precision isn’t just about avoiding errors—it’s a competitive necessity. EVs, with their tightly packed battery arrays and lightweight materials, demand flawless assembly. A misaligned component can compromise safety, efficiency, or aesthetics, leading to costly recalls.
Take Tesla’s 2022 recall of 1.1 million vehicles due to window calibration issues. BMW’s investment in BMW humanoid robot precision manufacturing aims to sidestep such pitfalls. In 2025, BMW’s permanent Figure 02 deployment at Spartanburg ensures BMW humanoid robot precision manufacturing sidesteps such risks, with autonomous operations hitting tolerances unmatched by human hands. By achieving tolerances 10x tighter than industry standards, BMW not only enhances reliability but also positions itself as a leader in quality—a key differentiator in the luxury EV market.
The Human-Robot Collaboration Model: Why It Works
Contrary to dystopian narratives, BMW’s robots are designed to augment, not replace, human workers. At the Leipzig plant, technicians oversee robot teams handling hazardous tasks like battery cell handling. By April 2025, Spartanburg technicians guide an autonomous Figure 02 fleet, proving BMW humanoid robot precision manufacturing thrives on human oversight and robotic muscle. Employees receive upskilling programs in robotics management, an initiative detailed in BMW’s training portal (/bmw-robotics-training).
Maria Schmidt, a 15-year BMW assembly veteran, shared: “Learning to work with these robots reignited my passion for the job. I now solve complex problems instead of repetitive tasks.”
Challenges and Ethical Considerations: Why Adoption Isn’t Universal
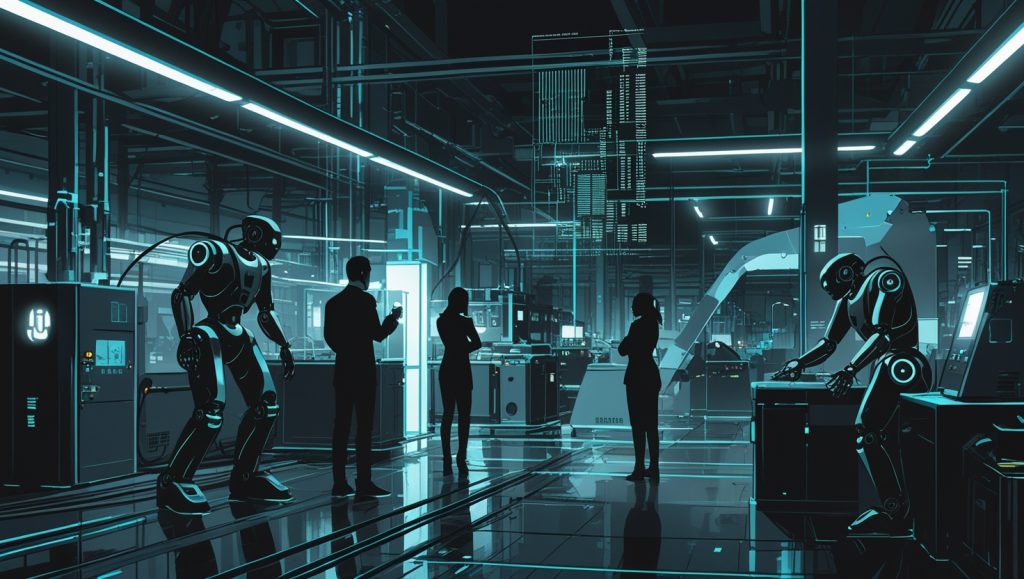
Despite their benefits, humanoid robots face hurdles. The upfront cost—$2-3 million per unit—is prohibitive for smaller manufacturers. Yet, Figure’s 2025 BotQ facility aims to scale production, potentially slashing costs as BMW humanoid robot precision manufacturing expands globally. Additionally, integrating these systems requires factory redesigns, a challenge BMW mitigated by modular upgrades at Spartanburg.
Ethically, concerns about job displacement persist. However, data from the International Federation of Robotics reveals that automation has created 1.7 million new roles globally since 2020, many in tech and maintenance. BMW’s partnership with local colleges to offer robotics certifications exemplifies how industries can balance innovation with workforce development. With Figure’s fleet intelligence growing in 2025, BMW humanoid robot precision manufacturing could create even more tech roles, balancing automation’s rise.
The Road Ahead: Industry 5.0 and Beyond
BMW’s robots are a harbinger of Industry 5.0, where AI, IoT, and human creativity converge. Future initiatives include:
- Swarm Robotics: Teams of robots collaborating on complex assemblies, inspired by NASA’s Mars rover teams. In 2025, Figure 02’s fleet intelligence hints at this future, with Spartanburg robots learning collectively to refine BMW Humanoid Robot Precision Manufacturing.
- Self-Optimizing Systems: AI that predicts supply chain disruptions and adjusts production in real-time. Figure’s Helix AI, powering 2025 operations, already nudges BMW Humanoid Robot Precision Manufacturing toward this predictive edge.
As outlined in McKinsey’s 2025 Industrial Automation Report, such technologies could boost global manufacturing output by $1.5 trillion by 2030.
Redefining Excellence in Automotive Manufacturing
BMW’s BMW humanoid robot precision manufacturing isn’t just a technical achievement—it’s a statement. By prioritizing precision, sustainability, and human empowerment, BMW is crafting a blueprint for the future of manufacturing. As competitors scramble to catch up, BMW’s blend of innovation and ethics positions it not just as a carmaker, but as a pioneer of industrial evolution. With Figure 02’s permanent 2025 rollout at Spartanburg, BMW humanoid robot precision manufacturing isn’t just a vision—it’s the new reality of automotive excellence.
For further insights, explore our analyses on AI in manufacturing. Dive into scalable robotics trends at Why Robot Subscription Services Are the Next Big Revenue Stream.