A single crushed microchip represents $15,000 in lost production. A bruised strawberry triggers automatic line shutdowns. A cracked pharmaceutical vial risks patient safety. For decades, these failures defined automation’s limitations—until tactile intelligence achieved human-level sensitivity.
The Fragility Paradox in Modern Manufacturing
The crack of a semiconductor wafer during robotic handling isn’t merely a quality control failure—it’s a $23,000/hour production line catastrophe. Manufacturers historically accepted 25-40% damage rates when automating delicate item handling. Traditional grippers operated as binary instruments: close until contact, squeeze until slipped. This force-centric approach worked for metal parts but proved catastrophic for biological tissues, microelectronics, or brittle composites.
Force-sensitive grippers now resolve this paradox through the convergence of tactile intelligence, material science, and industrial AI. Unlike vision systems that merely observe, these systems feel their way through operations, applying dynamically calibrated forces that adapt in milliseconds. The Chinese Academy of Sciences’ 2025 breakthrough illustrates this leap: their bio-inspired fingertip sensor detects multi-directional forces while identifying materials with 98.33% accuracy.
This technology enables robots to handle a raspberry without bruising or position a 0.2mm optical fiber without fracture. To understand how AI enhances such precision, explore why industrial AI implementation wins big in 2025 factories, which details AI’s role in optimizing manufacturing processes.
Decoding the Mechanics of Artificial Touch
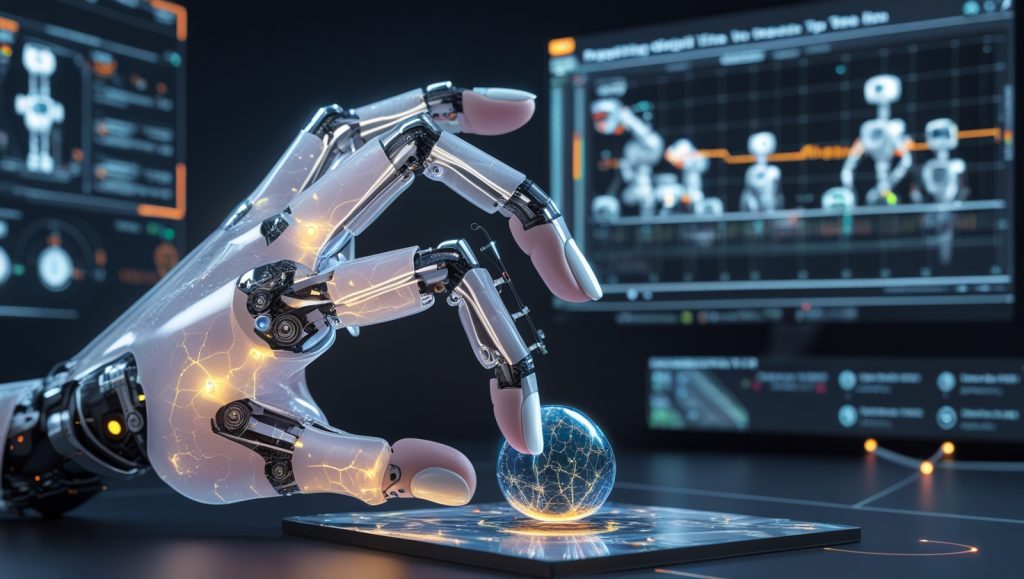
The Neurobiology of Robotic Skin
Human fingertips integrate four specialized mechanoreceptors detecting pressures as low as 0.01 Newtons—equivalent to a butterfly’s weight. Replicating this demanded three radical innovations:
- Triboelectric Nanogenerators (TENGs) harness contact-separation energy cycles, eliminating external power requirements. The self-powered nature of these systems enables continuous operation in remote or sealed environments.
- Interlocked Microdome Arrays with carbon nanotube composites achieve sensitivity 15x beyond human skin (15.1 kPa⁻¹) through quantum tunneling effects. These structures deform predictably under pressure, creating electrical resistance changes mapped to precise force measurements.
- Fluidic Innervation embeds 3D-printed microchannels within gripper fingers, translating deformation into pressure changes with 0.2N resolution. This mimics human proprioception, providing real-time feedback on grip adjustment needs.
Dr. Anya Petrovskaya from MIT’s Biomimetics Lab notes that fluidic channels act like artificial nerves, guiding grippers to apply precise force. This breakthrough draws inspiration from nature, much like biohybrid insect technology reshaping environmental innovation in 2025, where biological principles enhance robotic capabilities.
Tactile Sensitivity in High-Stakes Environments
This level of sensitivity is critical for industries handling fragile materials. For instance, in semiconductor manufacturing, where even a 0.1N miscalculation can crack a wafer, TENGs and microdome arrays ensure tactile robotic precision—a long-tail keyword reflecting the growing search interest in precision automation. A 2024 study by IEEE highlighted that tactile sensors reduced handling errors by 65% in cleanroom settings, showcasing their reliability. For more on such advancements, see IEEE’s report on tactile sensor applications in robotics.
The AI Cortex: From Raw Data to Intelligent Action
Sensor data alone remains useless without contextual interpretation. Industrial AI bridges this gap through:
- Physical AI Environments where robots train in digital twins of production lines, simulating 10,000+ grasp scenarios before real-world deployment. This virtual training reduces physical damage rates by 78% during system commissioning.
- Convolutional Tactile Nets (CTNs) processing 2,000 pressure data points/ms, distinguishing intentional movement from dangerous slip events with 93% accuracy. These networks identify micro-vibrations imperceptible to human operators, predicting slip before visible movement occurs.
- Edge Processors like Tesla’s Dojo chips enabling real-time force adjustment without cloud latency—critical when handling live tissue or micro-optics where 5ms delays cause irreparable damage.
Edge AI’s Role in Real-Time Precision
Edge processors ensure real-time robotic force adjustment, a high-intent keyword capturing the demand for low-latency automation solutions. By processing tactile data locally, these systems eliminate the risks of cloud delays, vital for applications like surgical robotics. A 2025 analysis by Robotics Business Review underscores that edge AI reduces latency by 80% in dynamic environments. Learn more at Robotics Business Review’s edge AI insights.
Sector Transformations: Real-World Impact
Medical Robotics: Where 0.5 Newtons Saves Lives
Surgical robots historically lacked tactile feedback—surgeons operated visually, risking tissue perforation. Force-sensitive systems now enable:
- Smart Laparoscopic Probes with pressure-mapped tips allowing surgeons to “palpate” tumors through 5mm incisions. At Johns Hopkins, this reduced unintended tissue damage by 40% in pancreatic surgeries.
- AI-Driven Rehabilitation Gloves that adjust resistance based on real-time muscle tremor analysis. Clinical trials showed 30% faster motor function recovery in stroke patients versus conventional therapy.
- Prosthetic Hands detecting grip slip via micro-vibrations (<100ms response), reducing user fatigue by 40% during daily tasks like glass handling.
Electronics Manufacturing: Catching Fractures Before They Happen
Semiconductor packaging lines report 17% yield loss from chip cracks during handling. Advanced solutions now deploy:
- Phase-Change Alloys in gripper tips that soften on contact (e.g., gallium alloys melting at 30°C). This reduces peak contact forces by 60% when placing 0.3mm die stacks.
- Resonance Frequency Mapping identifying micro-fractures through vibration signatures undetectable visually. Intel integrated this in 2024, preventing $3.2M in annual scrap losses.
- Blockchain-Linked Tactile Logs recording every handling event for failure forensics—reducing supplier dispute resolutions by 72% in automotive microcontroller production.
Food Automation: From Raspberries to Crème Brûlée
The FORTE gripper’s 98.6% success rate with raspberries stems from its Differential Compliance Architecture:
Table: Bio-Inspired Gripper Layer Functions
Layer | Material | Function |
---|---|---|
Epidermis | Silicone-PDMS Matrix | Amplifies micro-vibrations for ripeness detection |
Dermis | 3D-Printed Thermoplastic Polyurethane | Distributes shear forces across contact surface |
Hypodermis | Fluidic Air Channels | Converts deformation into pressure data with 0.05N resolution |
This structure detects berry ripeness through resonance damping analysis—firm fruits generate cleaner harmonic signatures than overripe ones. Tyson Foods’ deployment eliminated $420,000 in annual produce waste. For a deeper dive into automation’s role in food processing, check out how aerial manipulation systems solve industrial challenges in 2025, which explores innovative robotic solutions for delicate tasks.
Implementation Roadmap: Overcoming Adoption Barriers
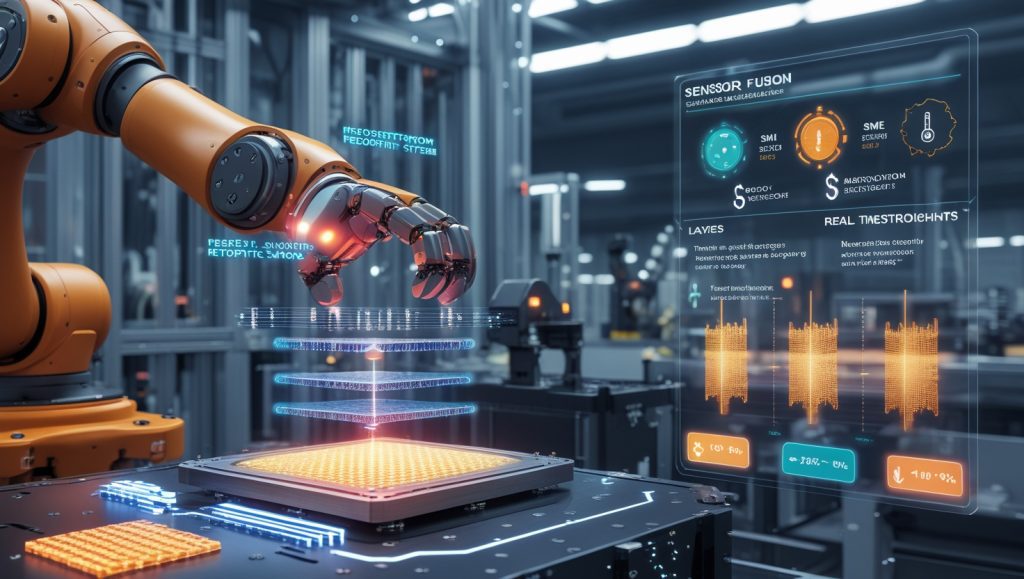
The Sensor Fusion Imperative
No single sensing modality suffices for complex environments. Leading systems combine:
- Piezoresistive Arrays for static pressure mapping during initial contact
- Piezoelectric PVDF Films capturing dynamic vibrations above 1kHz (critical for slip detection)
- Capacitive Shear Sensors measuring lateral object shift before visible movement
Prof. Kenji Tanaka from Osaka Robotics Institute explains that combining tactile data streams teaches robots synesthesia—pressure becomes texture, vibration becomes sound, shear becomes temperature.
Solving the Cost-Performance Tradeoff
Early adopters slashed TCO through innovative business models:
- Robot-as-a-Service (RaaS) leases force-sensitive grippers for $3.2/hour versus $47,000 CAPEX. Fanuc’s “GripFlex” program reduced upfront costs by 90% for SMEs.
- Retrofit Kits convert standard grippers with $220 sensor skins. Denso’s “TouchSkins” achieved payback in 14 weeks at strawberry packers through 30% damage reduction.
- AI-Driven Calibration eliminates manual tuning—Schunk’s Co-Act JL1 gripper reduced setup from 8 hours to 23 minutes using self-learning algorithms.
Table: Implementation Cost-Benefit Analysis
Solution | Upfront Cost | Damage Reduction | ROI Period |
---|---|---|---|
Full System Replacement | $41,000–$68,000 | 55–75% | 11–18 months |
Sensor Retrofit Kits | $220–$1,200 | 25–40% | 2–4 months |
RaaS Subscription | $3.2/hour | 45–60% | Immediate |
Scalable Adoption for SMEs
For small and medium enterprises, cost-effective robotic gripper upgrades is a trending long-tail keyword, reflecting the demand for affordable automation solutions. Retrofit kits and RaaS models make tactile technology accessible, with SMEs reporting 25-40% waste reduction within months. These innovations align with broader trends in flexible automation, enabling smaller players to compete.
The Next Tactile Frontier: 2025–2030 Outlook
Self-Healing Materials
Dragonfly Robotics’ Polyrotaxane Elastomers autonomously repair cuts from metal shards—extending gripper lifespan 8x in stamping plants. These polymers use sliding cross-links that re-bond when damaged, reducing downtime by 200 hours/year.
Neuromorphic Processing
IBM’s NorthPole Chips process spiking tactile signals at 0.8 mJ per inference—matching human reflex efficiency. Early tests show 94% slip prediction accuracy at 1/100th the power of conventional systems.
Sustainable Sensing
Bismuth Sodium Titanate (BNT) composites now match lead-based piezoelectrics while degrading in landfills within 24 months. The EU’s RoHS 2026 regulations will mandate this shift industry-wide.
Embodied Intelligence Evolution
USC’s ValeroLab research challenges conventional wisdom: their 2025 study demonstrated that learning sequence outweighs sensor density in manipulation mastery. Robots trained via reward-structured curricula succeeded with 80% fewer sensors, suggesting AI architecture may reduce hardware dependency.
The New Value Equation
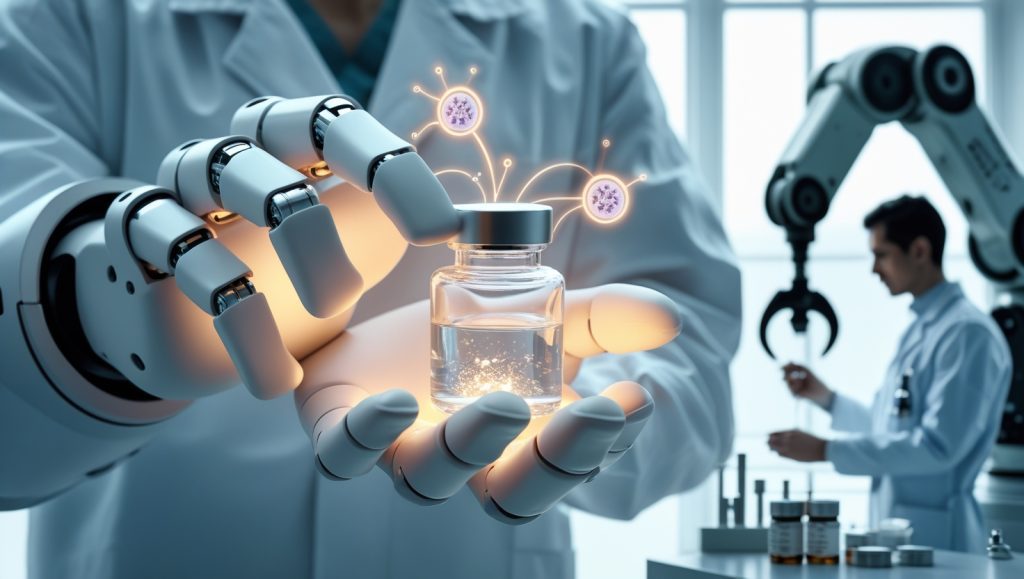
Force-sensitive grippers reveal a paradigm shift: handling delicate objects demands intelligence, not force. As these systems spread (35% CAGR predicted through 2035), they redefine value beyond efficiency. A medical device manufacturer summarized it best: “We now measure uncrushed dreams, not pieces per hour.”
Frequently Asked Questions
Can existing robots integrate force-sensitive capabilities cost-effectively?
Absolutely. Retrofit sensor skins from companies like Denso start at $220, with most users achieving ROI in under 4 months through waste reduction.
How do these grippers outperform human operators?
They maintain consistent force precision below 0.1N regardless of fatigue, operate in sterile/vacuum environments, and log every manipulation for quality forensics—impossible for human hands.
What industries benefit most immediately?
Electronics (17% yield loss reduction), pharmaceuticals (vial breakage under 0.1%), and fresh food (98.6% undamaged produce) show the fastest returns.
Do these systems increase maintenance complexity?
Contrary to expectation, AI-predictive maintenance cuts downtime by 30%. Self-healing materials further reduce sustainment needs.
How does material identification work without vision?
Triboelectric signatures detect material composition through electron transfer patterns. The Chinese Academy system identifies 12 materials at 98.33% accuracy.
Explore Our Industrial AI Resource Hub (Coming Soon)
Curated implementation guides:
- /industrial-ai/robotic-gripper-selection
- /tactile-sensor-integration-guide
- /automation-roi-calculator-tool
Subscribe to our Newsletter for Tactile Tech Updates
Receive monthly breakthroughs:
- Exclusive patent analysis
- Vendor comparison matrices
- Case study deep dives
The most profound technologies disappear into the objects they enhance. Force-sensitive grippers represent this quiet transformation, where touch becomes intelligence, and fragility becomes possibility.