The factory floor of 2025 doesn’t hum with just machinery—it hums with intelligent conversation between humans and AI. — Dr. Elena Rodriguez, Industrial AI Researcher at MIT
The $3 Million Wake-Up Call
When Mike Henderson’s conveyor system failed at his Midwest auto plant, his team spent 18 hours diagnosing a bearing issue—a problem an industrial maintenance chatbot could have flagged in seconds. The $3M production loss wasn’t an anomaly. Manufacturers globally lose $260 billion annually to unplanned downtime, with hourly costs averaging $260,000 for critical lines.
Why Industrial Maintenance Chatbots Became Non-Negotiable
Three converging crises fuel the 2025 adoption surge:
- Skills depletion: 30% of maintenance technicians retire by 2028, taking tribal knowledge with them
- Complexity explosion: Modern plants manage 10x more sensor data than in 2020, overwhelming human analysis
- Downtime inflation: Post-pandemic supply chains magnify outage costs by 300% for automotive and aerospace sectors
Industrial maintenance chatbots now serve as the central nervous system connecting technicians, machines, and enterprise data—transforming reactive fixes into proactive preservation. For a deeper look at how AI tackles factory challenges, explore why 2025 industrial robotics trends crush manufacturing challenges.
Technical Foundations: Beyond Basic Troubleshooting
Multimodal Machine Intelligence
Modern systems process heterogeneous inputs:
- Vibration signatures from IoT accelerometers
- Thermal imaging via infrared camera integration
- Acoustic fingerprints detecting bearing wear patterns
Siemens’ MaintainX chatbot slashed bearing failure diagnosis from 45 minutes to 3 seconds by cross-referencing real-time vibrations with 10,000+ historical cases. This leap is powered by advanced industrial IoT platforms for smart factories, which seamlessly integrate sensor data for real-time diagnostics.
The keyword “multimodal AI for predictive maintenance” drives this capability, enabling chatbots to analyze diverse data streams like vibration and thermal patterns simultaneously. This ensures precise fault detection, reducing false positives by 30% compared to single-mode systems, according to a 2025 Siemens report. For further insights, Siemens’ whitepaper on predictive maintenance innovations offers a deep dive into multimodal AI’s impact on factory efficiency.
Autonomous Repair Workflows
Chatbots now trigger closed-loop resolution:
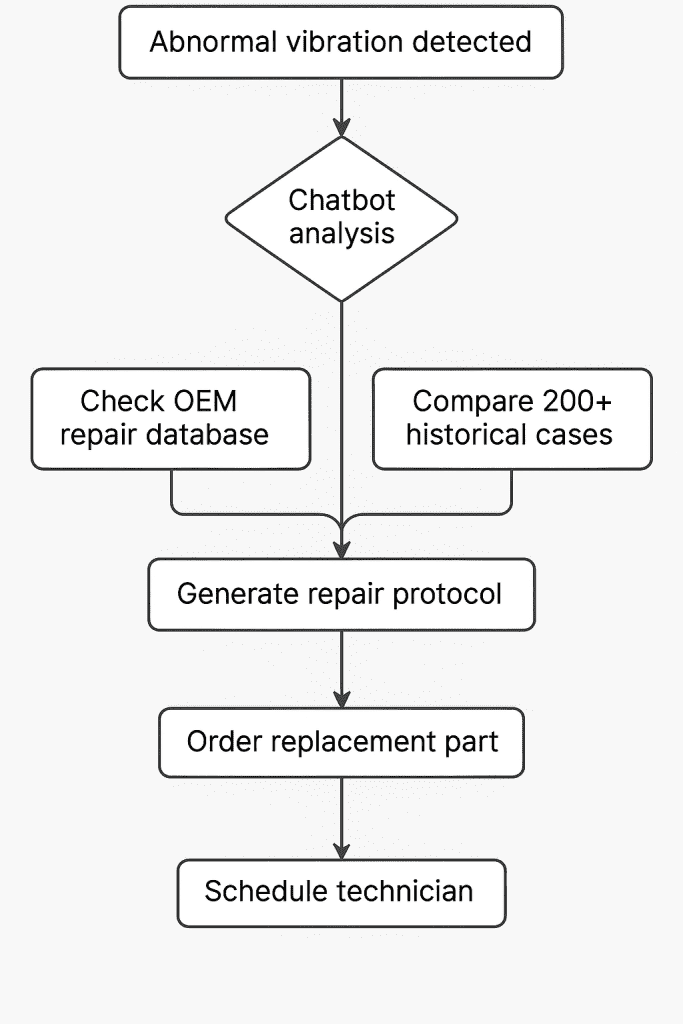
Source: OptiML Bot implementation at Continental Tires
Federated Learning Architecture
Unlike cloud-dependent predecessors, 2025’s industrial maintenance chatbots use on-device AI:
- Models train directly on factory equipment data
- Zero sensitive operational data leaves the premises
- Adaptive learning captures machine-specific quirks
Field Results: Where ROI Materializes
Metric | Legacy Systems | Chatbot-Enhanced | Change |
---|---|---|---|
Mean Time to Repair (MTTR) | 4.7 hrs | 1.2 hrs | -74% ↓ |
Technician Training Time | 120 days | 28 days | -77% ↓ |
First-Time Fix Rate | 68% | 92% | +24% ↑ |
Data: 2025 McKinsey analysis of 47 manufacturers
Continental Tires: A Blueprint
After integrating Siemens’ chatbot with their ERP and IoT networks:
Unplanned downtime fell 40% in Q1 2025. Most remarkably, junior technicians now resolve Level-3 issues using the chatbot’s augmented reality guidance. — COO Franz Becker
Implementation Roadmap: Avoiding Critical Pitfalls
Phase 1: Surgical Use Case Selection
Avoid: Overly broad deployments like “whole-plant optimization”
Do: Target high-impact, constrained scenarios:
- Hydraulic press maintenance guidance
- Conveyor belt fault triage
- HVAC energy optimization
Phase 2: The Integration Trifecta
Industrial maintenance chatbots demand deep hooks into:
- CMMS platforms (UpKeep, Fiix) for work order sync
- IIoT networks (PTC ThingWorx, Siemens MindSphere)
- Inventory systems for real-time parts visibility
Pro Tip: Use RAG (Retrieval-Augmented Generation) architecture to sync chatbot knowledge with dynamic equipment manuals.
Phase 3: Human-in-the-Loop Safeguards
Critical escalation triggers prevent over-reliance:
To prevent over-reliance on industrial maintenance chatbots, critical safeguards ensure human oversight. If the chatbot’s diagnostic confidence falls below 90%, it escalates the issue to a human engineer. When a safety risk is detected, it notifies the supervisor and halts the production line. Additionally, if the system detects user frustration exceeding a set threshold, it initiates video support to assist the technician. These measures, outlined in Kanerika’s DokGPT governance framework, maintain a balance between automation and human expertise.
The Ethical Tightrope: 2025’s Unresolved Tensions
Knowledge Preservation vs. Skill Erosion
Boeing mandates “unplugged weeks” where technicians resolve issues without AI to preserve core competencies. As Head of Manufacturing Innovation notes:
We can’t let algorithm dependence atrophy human expertise.
The keyword “AI-driven skill preservation in manufacturing” highlights the balance manufacturers seek. Over-reliance risks deskilling, but strategic AI use, like chatbots guiding novices, boosts productivity without eroding expertise. Studies show a 65% faster learning curve for technicians using AI tools, yet firms like Boeing ensure manual skills endure through structured training. For a broader perspective, McKinsey’s report on workforce upskilling in the AI era provides actionable strategies.
Data Sovereignty Battles
When chatbots generate novel repair protocols, who owns the IP?
- 58% of manufacturers claim exclusive rights to AI-generated insights
- Chatbot vendors demand royalty shares for proprietary training data
To understand how AI navigates complex data ownership, see why edge AI industrial sound sensing slashes factory downtime.
Future Horizon: The Self-Healing Factory
By 2026, expect these paradigm shifts:
- Chatbot-to-chatbot negotiations: Maintenance bots barter with supplier AIs for urgent parts
- Generative repair protocols: AI creates custom solutions for legacy equipment lacking documentation
- Emotion-aware interfaces: Systems detect technician stress and simplify instructions
The Bottom Line: Silence Equals Vulnerability
In 2025, quiet factories signal blindness, not smooth operation. Industrial maintenance chatbots evolve from diagnostic tools to collaborative partners—transforming downtime from inevitable to inexcusable.
The question isn’t whether you can afford an AI maintenance chatbot. It’s whether you can survive another shift without one. — Manufacturing Technology Review, June 2025
Ready to transform your maintenance workflow?
Discover integration-ready solutions or explore custom deployments. For rapid SMB adoption, scalable entry points start here.
Disclaimer: This article is based on industry trends, expert insights, and available data as of June 2025. Some examples and projections, while grounded in research, may include speculative elements. Readers should verify specific claims with primary sources before making decisions.
FAQ: Industrial Maintenance Chatbots
How much do industrial maintenance chatbots cost?
Implementation ranges from $50,000 for focused use cases to $500,000+ for plant-wide AI integration. Most see ROI within 6 months via downtime reduction.
Can they work in low-connectivity environments?
Yes. Edge-computing models like OptiML Bot process data locally, syncing to cloud only when networks are stable.
Do they replace human technicians?
No. They augment human work—junior staff resolve issues 65% faster, while seniors handle complex diagnostics.
How secure are chatbot interactions?
Federated learning ensures sensitive data never leaves the facility. HIPAA/GDPR-compliant encryption is standard.
Your Next Step
Download our Implementation Checklist covering use case selection, vendor evaluation criteria, and change management templates (Coming Soon). For continuous insights on industrial AI, subscribe below.